In TTX (sede centrale in Wisconsin, USA), ci dedichiamo alla progettazione e alla produzione di linee industriali di trattamento delle superfici, sistemi di movimentazione dei materiali, impianti per il trattamento delle acque di processo e delle acque reflue. In questo articolo vogliamo condividere una delle nostre più recenti innovazioni, nel campo dei sistemi di movimentazione dei materiali, applicabile in molti settori industriali e, naturalmente, nell’industria dei trattamenti industriali delle superfici. Lo chiamiamo TTXACC®, Automated Carrier Conveyor, essendo un sistema di trasporto completamente automatico. Faremo una presentazione generale, con l’obiettivo di far conoscere un’innovazione industriale che riteniamo importante, convinti che sia vantaggioso per tutti raggiungere livelli tecnologici più elevati.
Il sistema TTX-ACC® è una soluzione flessibile, sicura ed economica, per la movimentazione dei materiali. Può essere utilizzato per qualsiasi tipo di produzione, finitura e assemblaggio, anche connettendo tutte queste fasi contemporaneamente: ha molteplici applicazioni.
L’abbiamo progettato tenendo conto delle diverse sfide poste dai nostri clienti, il che ci ha permesso di migliorare e innovare ed espandere le opzioni che offriamo per risolvere le loro esigenze, a partire dai sistemi di trattamento delle superfici e verniciatura, coinvolgendo tutti i processi precedenti e quelli posteriori. Quella che presentiamo è una realtà industrializzata, non un mero concetto di innovazione: è una soluzione già presente sul mercato, di cui esistono applicazioni concrete, sviluppate con clienti con esigenze specifiche e diverse, e che ci ha portato risultati sorprendentemente positivi.
L’ARCHITETTURA CONCETTUALE
Fondamentalmente, il sistema è stato sviluppato intorno a concetti semplici: travi ad “I”, assenza della o delle catene. Di fatto, il cuore del sistema è la barra di trasporto (di pezzi o bilancelle) totalmente autonoma, con trazione su ruote, guidato da una monorotaia composta da travi ad “I” e semplici scambi, come siamo abituati a vedere nelle linee ferroviarie.
Il concetto del trasportatore senza catena non è una novità, ciò che è nuovo è il concetto di estrema semplificazione e gestione che ci ha guidato nel suo sviluppo, che porta più benefici rispetto ai “mal di testa” tipici dei sistemi di trasporto complessi. Per creare una soluzione di valore, quando abbiamo iniziato a progettare il TTX-ACC® ci siamo posti 4 obiettivi, che coincidono con 4 requisiti principali che le aziende con cui abbiamo parlato hanno confermato considerare molto importanti:
SICUREZZA
Intesa come sicurezza dei lavoratori, delle attrezzature e dei prodotti che vengono trasportati. Un trasportatore è necessario quando dobbiamo spostare qualcosa da un lato all’altro in modo autonomo, quindi deve essere sicuro al 100% per le persone, per le attrezzature che si trovano intorno al mezzo di trasporto e, naturalmente, per il carico trasportato.
SOSTENIBILITÀ
Che utilizzi le risorse, sia energetiche che umane, in modo efficiente e che consenta di utilizzare in modo efficace macchine, attrezzature e prodotti che compongono il nostro processo industriale, compreso, naturalmente, il sistema di verniciatura. Che possa minimizzare gli interventi di manutenzione e che, allo stesso tempo, possa prendere autonomamente alcune decisioni e svolgere da sola compiti d’interesse principale.
FLESSIBILITÀ
Dev’essere un sistema flessibile, fattore molto importante in questo momento, e consentire il semplice adattamento alle possibili modifiche future. Per progettare linee di produzione efficienti, infatti, è necessario e fondamentale rispondere alle esigenze attuali, ma il sistema deve permettere di risolvere in modo altrettanto efficiente – quando se ne presenterà la necessità – i compiti di trasporto di beni e processi diversi rispetto a quelli odierni: TTX-ACC® è stato progettato in modo da potersi adattare con precisione ai cambiamenti del futuro, anche in termini di crescita ed espansione delle attività.
MANUTENZIONE
La programmazione e il calcolo delle risorse per la manutenzione non vengono solitamente effettuate al momento di decidere l’investimento, ma quando il sistema è già stato installato e messo in funzione. Al contrario, il TTX-ACC® è progettato per ridurre al minimo la manutenzione, automatizzare la maggior parte delle relative operazioni, in breve, non per avere costi nascosti.
LA BARRA DI TRASPORTO
Ebbene, tenendo conto dei 4 obiettivi sopra menzionati, approfondiamo qualche informazione relativa a questo innovativo sistema di movimentazione materiali.
Ogni barra di trasporto (portapezzi o bilancelle, di seguito “barra”) ha un proprio controllo di coppia, cioè il suo motore con la sua batteria (che fornisce l’energia di movimento). Ogni barra è dotata di un sistema di sicurezza (scanner/laser, per il rilevamento tempestivo di potenziali collisioni) che la blocca istantaneamente, quando necessario, senza fermare le barre operative nelle altre zone della linea. Ciascuna barra dispone inoltre di spia luminosa (LED) e allarmi audiovisivi. Diamo un’occhiata più da vicino: la fig. 5 mostra una vista laterale della barra.
Come detto, ognuna ha il proprio controllo di coppia individuale. Abbiamo già visto altre soluzioni di trasporto e movimentazione dei materiali senza catena, dove vengono utilizzati altri meccanismi di propulsione, di solito motori installati lungo la linea, che producono esattamente il movimento che stiamo cercando. Il nostro progetto prevede invece che ogni barra abbia il proprio motore, il che significa che è totalmente indipendente: non abbiamo bisogno di avere l’intera linea di lavoro – o l’intera linea di motori – in movimento. In questo modo la barra è non solo totalmente indipendente, ma anche totalmente programmabile, in modo che vada dove ci serve e alla velocità che vogliamo. Ovviamente, ciascuna barra segnala il suo movimento sullo schermo di controllo e programmazione e, per la sicurezza dei lavoratori dell’area in cui è installato il sistema, segnala il movimento visivamente tramite luce di sicurezza e allarme acustico (come siamo abituati a vedere e ascoltare in fabbrica con i muletti). Un sistema di rilevamento preventivo di possibili ostacoli (lavora anche il carico eccede le dimensioni della barra), ferma la barra per tempo (o la fa spostare o retrocedere, secondo quanto programmato).
Il sistema è silenzioso. Ci si dimentica del concerto delle catene (per alcuni il rumore delle catene in fabbrica è musica, dovranno farne a meno!), del circuito di lubrificazione e di oli e grassi che, nelle linee di finitura, possono compromettere la qualità delle superfici dei pezzi trasportati.
ENERGIA
Il sistema, o meglio ogni barra, dev’essere alimentata elettricamente. Per questo è stato progettato un alimentatore chiuso: non c’è una linea elettrica (come nel caso di un treno o una metropolitana): l’alimentazione avviene con batterie individuali (per barra), completamente chiuse, isolate e impermeabili, completamente sicure (non possono generare scariche o cortocircuiti): il motore di ogni barra usa, infatti, l’energia di una batteria al litio ricaricabile (tipo AGM, senza acido in fase liquida, che invece impregna un materassino di microfibra di vetro).
Queste batterie si caricano 5 volte più velocemente e sono molto più leggere di una batteria “allagata” tradizionale, non soffrono del problema della solfatazione, e non sono sensibili alle vibrazioni. Fornisce meno energia di una batteria tradizionale, ma offrono una resistenza molto bassa, quindi erogano molta corrente nell’unità di tempo, il che è un grande vantaggio nei tipici cicli di avvio/arresto della barra. Sono batterie che permettono di progettare sistemi molto agili, efficaci, modulari e leggeri (ogni barra può così caricare più peso).
Tenendo conto della totale autonomia di ogni barra e dell’architettura fisica del sistema di trasporto (travi a I), risulterà più chiaro perché il sistema è completamente modulare e facilmente espandibile.
Naturalmente, anche un trasportatore a catena può essere ampliato o modificato, ma si tratta sicuramente di un’operazione più complessa.
Ciascuna catena, inoltre, ha dei limiti in termini di aumento di peso, e normalmente devono essere modificati o cambiati anche il motore o i motori.
Il nostro sistema permette semplicemente di inserire più barre a seconda delle necessità, e senza fermare tutto il sistema di trasporto. Se la linea ha bisogno di essere estesa, richiede interventi molto semplici, è sufficiente aggiungere alcune travi con la loro struttura di supporto, una rapida modifica al lay-out nel centro di programmazione e controllo, e questo è tutto.
L’uso dell’energia di ogni barra è sempre la più efficiente (è gestita da inverter) ed è indipendente dalle dimensioni della linea. Ogni barra è stata progettata per passare al di fuori delle fasi attive (tunnel di granigliatura, di pretrattamento, e forni).
Nel caso dei forni, ciò significa che non si consuma calore per riscaldare la catena, un inutile consumo di energia, ancora più vero quando siamo di fronte a trasportatori a catena per carichi molto pesanti.
CARICHI E CICLI PERSONALIZZATI
Siccome ogni barra è completamente indipendente, ne viene semplificato il lavoro di programmazione del reparto di trattamento delle superfici, ancor più se siamo di fronte a una linea di trasporto che collega i diversi reparti di produzione, trattamento, assemblaggio.
La flessibilità che offre un sistema di barre indipendenti, in particolare se lo confrontiamo con un sistema monorotaia, è chiara e non ha bisogno di molte spiegazioni: il movimento e la velocità di ogni barra non dipende dalla catena, possiamo fermarne una per il tempo che ci serve – o metterla in un polmone, di fianco alla linea o sopra o sotto – mentre le altre barre continuano il loro lavoro; possiamo rallentarla o velocizzarla, il tutto senza dover modificare gli altri flussi di barre. Questo significa, inoltre, che non è necessario avere barre vuote in linea.
Rispetto a un sistema Power&Free (che pure produciamo), il fattore di differenza è la semplificazione dell’architettura del sistema e la riduzione degli spazi occupati: non ci sono circuiti di ritorno delle catene, e non c’è complessità dei meccanismi; non c’è bisogno di dividere la linea in circuiti in base alla loro velocità (tipicamente, “lento” e “veloce”, eventualmente un terzo circuito “medio”). Il sistema TTX-ACC® è composto da binari e scambi, se si vuole, ascensori/discensori (evitando le salite e discese dei convogliatori tradizionali), tutti realizzati con travi a “I”. Le barre possono muoversi lateralmente, fare curve a 90°, spostarsi su un’altra “rotaia” per mezzo di semplici intersezioni, muoversi verticalmente. Lo spazio occupato si ottimizza totalmente. La velocità (e la direzione) di ogni barra è programmabile, una a una.
La ricarica delle batterie si effettua secondo un principio “opportunista”, ogni barra sfrutta le zone di ricarica automatica quando più conveniente, ad esempio, mentre si sta fermi per rispettare i tempi di una particolare fase del processo. Nel caso di linee a vasche, i sistemi tradizionali usano uno o più carriponte dotati di gru che permettono l’immersione dei pezzi, lasciando la barre sulle vasche di processo, e mentre si compie il tempo di ciclo previsto dalla vasca, il carroponte va a prendere un altra barra per depositarla in un’altra vasca. A volte è necessario utilizzare 2 o più carriponte, il che complica la programmazione e, peggio ancora, la riprogrammazione, quando necessario a causa di un cambiamento nel tipo di carica (tipo di pezzi) o di processo. Con il sistema TTX-ACC®, semplicemente non ci sono carriponte, ogni barra è indipendente e va secondo il suo programma.
Queste caratteristiche permettono da un lato di rendere flessibile la progettazione dell’impianto, dall’altro di programmare ogni barra secondo la sua specifica ricetta di produzione. I tempi di fermo macchina si riducono drasticamente, in quanto ogni barra può essere programmata in modo indipendente e si può impostare il programma più efficiente in base alle diverse fasi di ogni processo o carica. Con questo sistema non ci sono vuoti nel flusso produttivo.
PRECISIONE
Ogni barra si muove in modo definito e preciso (la precisione è nell’ordine del millimetro). Precisione e accuratezza di posizionamento sono di fondamentale importanza, in particolare nei processi ad alta automazione robotizzata. La stessa precisione si ottiene anche con i sistemi a catena, con molto sforzo, molti calcoli e molta manutenzione (recupero della dilatazione delle catene, consumo del tenditore e altro ancora).
MANUTENZIONE
Il sistema TTX-ACC® non richiede una manutenzione complessa e costosa, come quella dei trasportatori a catena: non ci sono lubrificatori per catene, non ci sono spazzole per pulire la catena o le guide, l’infrastruttura pneumatica ed elettrica è minima (scambi, discensori). Le operazioni di manutenzione di questo sistema sono minime, vengono effettuate in uno “binario di manutenzione” posto in un ramo del circuito principale o in specifiche aree di tale circuito. In questa(e) zona(e) ogni barra può essere rimosso o reinserito nel circuito. I binari di manutenzione sono utilizzati anche per facilitare, quando necessario, le operazioni d’omologazione (o riomologazione) delle diverse fasi del processo: la barra esce dal circuito principale, si ferma per consentire di effettuare le necessarie misurazioni e valutazioni e puó rientrare nel flusso di processo per passare alla fase seguente. I ricambi per la manutenzione ordinaria e straordinaria sono facilmente reperibili sul mercato, poiché la politica di progettazione del sistema ha previsto l’uso di componenti standard, proprio per facilitare queste operazioni. Il sistema di programmazione e gestione del TTXACC®, semplice e intuitivo (con interfaccia grafica), offre anche la possibilità di tracciare e memorizzare lo storico di ogni suo componente, in modo da regolare continuamente il piano di manutenzione, compresa la manutenzione preventiva. L’infrastruttura, come abbiamo detto, permette di effettuare modifiche (ed espansione) in modo molto semplice, dato che il circuito è fondamentalmente una struttura di supporto con pochi elementi mobili (scambi, discensori), e richiede una semplice modifica del software relativamente al nuovo lay-out.
OPERATIVITÀ
Il sistema funziona con infrastruttura elettronica basica – rete ethernet wireless a circuito chiuso – encoder lineare e sensore per il posizionamento preciso. Tutti i dati relativi sono visualizzati sia sullo schermo della stazione di controllo, sia su smartphone. Il software di programmazione e controllo è completamente digitale e può gestire tutte le interfacce dati con i sistemi che consentono la registrazione e la trasmissione dei dati per i4.0 (ACC® nasce integrando le tecnologie abilitanti per l’i4.0, offrendo una totale trasparenza sulla movimentazione dei materiali che attraversano i flussi dei processi produttivi). Puó essere interfacciato, per esempio, al sistema IT di fabbrica ed essere programmato tramite ERP (Enterprise resource planning).
Il sistema di programmazione e gestione delle barre ha la possibilità di prendere alcune decisioni autonomamente: in caso di rilevamento di un ostacolo, ad esempio, la barra può fermarsi o invertire la direzione e comunicare alle altre barre la nuova situazione, perché agiscano di conseguenza (scegliendo tra un universo di alternative previste). PLC ed Ethernet di ogni caricabatterie sono in continua comunicazione via wi-fi: inviano e ricevono informazioni di destinazione e logica di routing, rapporti di stato e, quando necessario, altre istruzioni di funzioni speciali.
Un software di programmazione veramente userfriendly con HDMI (High Definition Multimedia Interface) permette di programmare e modificare il sistema anche senza avere conoscenze specifiche di programmazione (naturalmente è richiesta la conoscenza specifica della logica delle diverse fasi del processo).
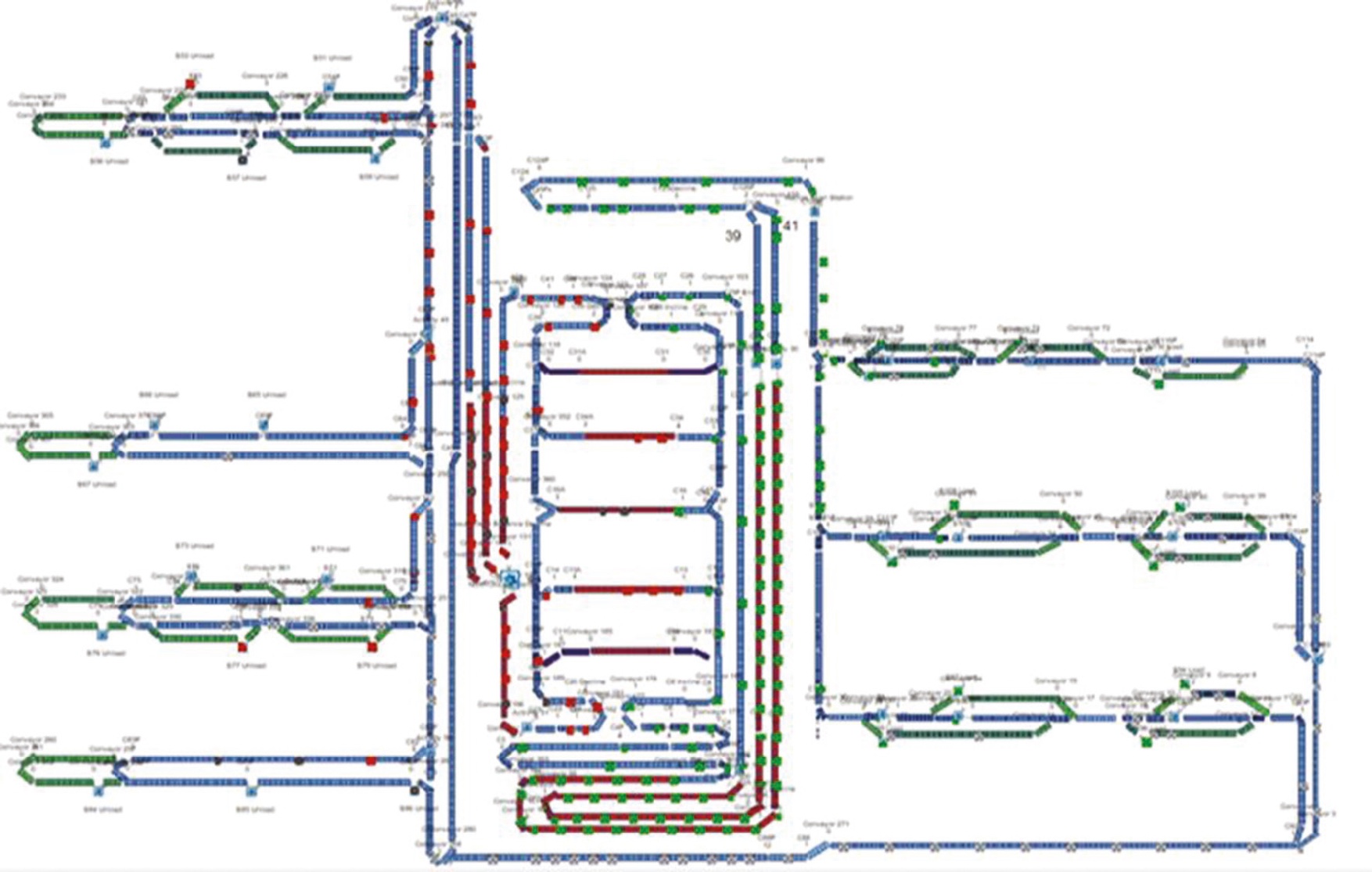
Nella figura si vede il layout di un caso reale di utilizzo del sistema TTX-ACC®. In questo caso è stato progettato per organizzare tutta la logistica del flusso produttivo, a partire dalle fasi di produzione, passando dalla zona di trattamento delle superfici, fino all’assemblaggio finale.
In conclusione, riteniamo che la movimentazione dei materiali costituisca un’area di opportunità per ottimizzare e tracciare qualsiasi processo di produzione, compresi naturalmente i processi di trattamento delle superfici. La soluzione che offriamo è caratterizzata da altissima flessibilità d’uso e di programmazione, e in TTX (EE.UU, Messico, Brasile) siamo aperti ad analizzare, insieme, casi specifici che possono presentarsi in ogni fabbrica, sfruttando l’agile architettura di progettazione che è stata sviluppata proprio per questo scopo.