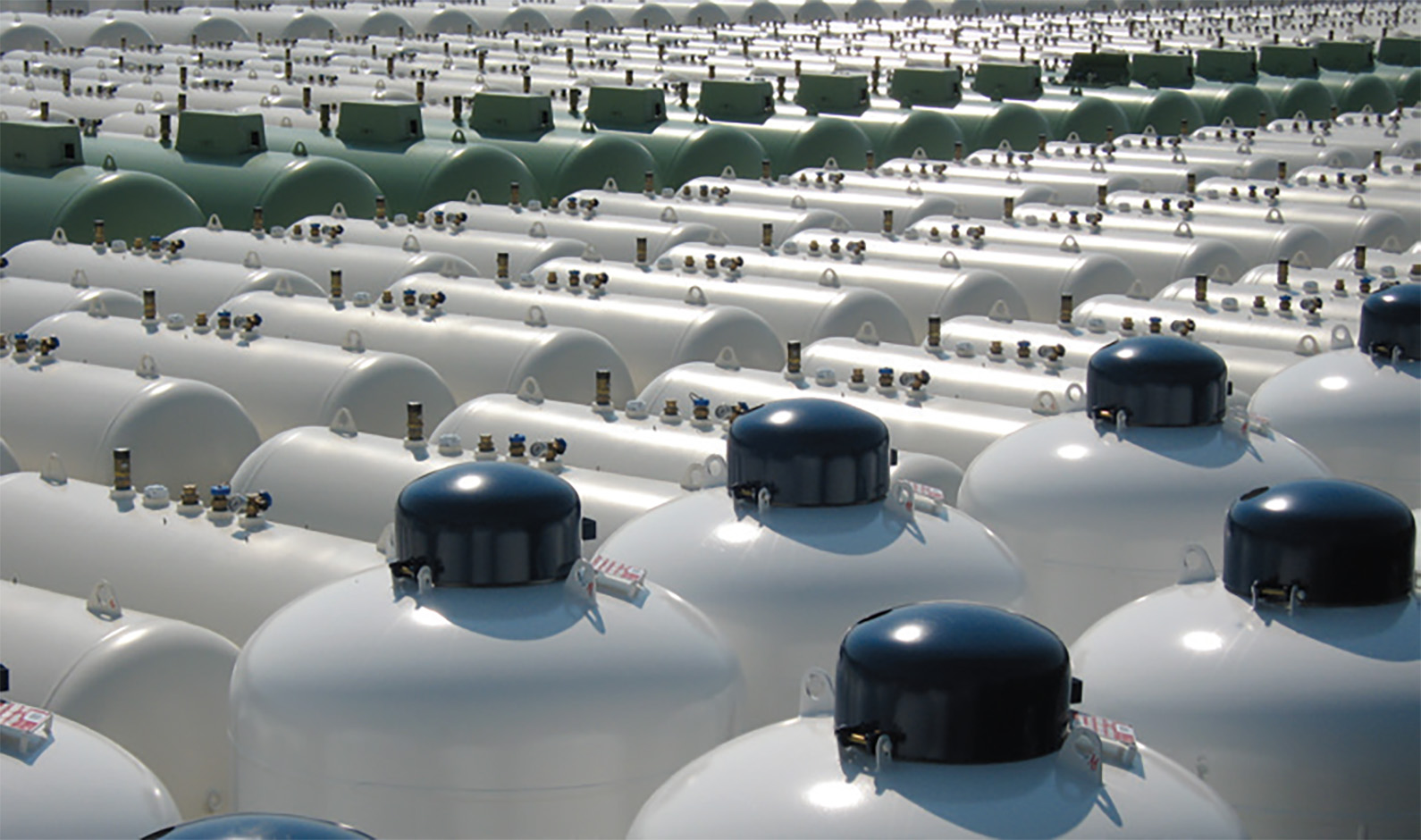
OLTRE 50 ANNI FA LA ANTONIO MERLONI PRESSURE VESSELS HA INIZIATO LA PRODUZIONE DI BOMBOLE DI GAS PROPANO LIQUIDO, AGGIUNGENDO NEGLI ANNI ’70 LA PRODUZIONE DI SERBATOI DI PICCOLA E GRANDE CAPACITÀ.
Oggi, con siti produttivi a Matelica e Sassoferrato, in Italia, l’azienda serve più di 1.200 clienti in 48 paesi ed è uno dei maggiori produttori europei di bombole e serbatoi per lo stoccaggio di GPL. Tutti i loro prodotti richiedono il rispetto di severi standard costruttivi e la conformità alla Direttiva europea UNI EN 1442 2010/35/UE per le bombole o alla Direttiva europea per apparecchiature in pressione (PED) 2014/68/UE UNI EN 12542 per i serbatoi.
Nel 2020, sotto la nuova guida di Paolo Sparvoli e il supporto di un team PPG con sede a Verbania, la Antonio Merloni ha iniziato ad attuare un programma di rinnovamento e ammodernamento degli impianti per aumentare la produttività e la qualità del prodotto, migliorare le strutture e ridurne l’impatto ambientale. La prima fase del processo è iniziata con la transizione delle linee di verniciatura dei serbatoi fuori terra e interrati – con capacità da 290 a 3.000 litri (da 77 a 793 galloni), diametri da 800 a 1.200 mm (da 31 a 47 pollici) e altezze fino a 3 metri (9,8 piedi) – dai rivestimenti liquidi a quelli in polvere.
«La sostenibilità è uno dei nostri valori aziendali, che richiede il rispetto dell’ambiente e la valorizzazione dei luoghi di lavoro», ha affermato Valeria Tassotti, responsabile tecnico di Merloni. «Poiché i rivestimenti in polvere sono realizzati senza solventi, che rilasciano composti organici volatili dannosi, è una tecnologia più sostenibile ed elimina la necessità di gestire le acque reflue pericolose che derivano dal processo di verniciatura a liquido». Ma la transizione ha avuto anche vantaggi che andavano oltre la buona gestione dell’ambiente. Secondo Valeria, il cambiamento ha anche migliorato il benessere generale e la produttività dei lavoratori dell’impianto che ora sono in grado di operare in un ambiente più pulito.
MIGLIORAMENTO DEL PROCESSO E DEL CONTROLLO DI QUALITÀ
La verniciatura a polvere è un processo di finitura superficiale in più fasi e Antonio Merloni ha investito in un sistema di verniciatura in linea completamente automatizzato per misurare tutti i parametri operativi dell’impianto e, di conseguenza, migliorare la qualità della finitura.
«Con le vernici in polvere, possiamo automatizzare ogni fase dell’applicazione e fare affidamento sulla parametrizzazione dell’impianto per un controllo più accurato dei dati del flusso di produzione rispetto alla verniciatura a liquido», ha aggiunto Valeria. «Possiamo monitorare i dati sulle temperature e i tempi di tutte le fasi applicative, ad esempio, ma anche la velocità di traslazione e rotazione del pezzo che ci aiuta a individuare rapidamente le cause di eventuali difetti di qualità».
Per Antonio Merloni il successo del progetto è dipeso soprattutto dall’affidabilità dell’azienda che ha installato il nuovo impianto di verniciatura e del fornitore di polveri, oltre che dalla loro capacità di collaborazione.
Ogni anno, Antonio Merloni Pressure Vessel produce un milione di piccole bombole per uso domestico con una capacità da 5 a 25 kg nello stabilimento di Sassoferrato, in Italia. Oltre alle differenze dimensionali, questi cilindri verniciati a polvere hanno anche cicli di verniciatura, colori e requisiti di protezione diversi rispetto ai serbatoi.
Lo stabilimento di Verbania, in Italia, che un tempo faceva parte dell’attività di produzione polveri di Arsonsisi prima che PPG lo acquisisse lo scorso anno, forniva all’impianto vernici in polvere poliestere per piccoli cilindri per uso domestico già dal 2015.
Con la decisione di sostituire le vernici liquide con quelle in polvere sui piccoli serbatoi prodotti nello stabilimento di Matelica, Antonio Merloni aveva bisogno di un nuovo impianto di verniciatura a polvere e di nuove polveri personalizzate per i piccoli serbatoi ivi prodotti. PPG si è dimostrata il partner giusto per il progetto. Antonio Merloni Pressure Vessels ha inaugurato nella primavera del 2022 il suo nuovo impianto di verniciatura a polvere completamente automatizzato presso lo stabilimento di Matelica.
«In un nuovo impianto di verniciatura così grande, ci vuole un po’ prima di raggiungere un flusso di produzione costante, poiché è necessario risolvere eventuali problemi iniziali derivanti dall’impianto stesso o dalle condizioni della polvere prima di impostare i parametri ottimali dell’impianto», ha spiegato Fabrizio Delgrande, tecnico commerciale PPG per le vernici in polvere. «Il laboratorio R&D delle vernici a polvere di PPG ha effettuato diversi test prima di finalizzare le formule del prodotto».
I RIVESTIMENTI ANTICORROSIVI SVOLGONO UN RUOLO FONDAMENTALE PER LA SICUREZZA
Gli standard nel settore della produzione di recipienti a pressione richiedono che la finitura finale di un serbatoio sia resistente sia alla corrosione del suolo che atmosferica. Il processo di rivestimento gioca un ruolo chiave, insieme al pretrattamento di sabbiatura, per prevenire la corrosione e garantire la sicurezza del serbatoio. Sia la lamiera che la saldatura della struttura del serbatoio forniscono resistenza alla pressione.
Ma il serbatoio deve anche resistere alla corrosione del suolo e dell’atmosfera, ed è qui che la finitura fa la differenza.
«La corrosione rende la lamiera più sottile e meno resistente alla pressione. Se il serbatoio è ben protetto, funzionerà in sicurezza nel modo in cui è stato progettato», ha spiegato Valeria.
Per i serbatoi interrati, PPG ha sviluppato e personalizzato le polveri epossidiche in base al sistema di rivestimento del cliente e ai colori dei serbatoi.
«Antonio Merloni utilizza la tecnologia epossidica monostrato fusion-bonded per la protezione dalla corrosione delle condotte sotterranee in acciaio utilizzate per il trasporto di gas, petrolio e acqua», spiega Fabrizio. «Questi tubi, come i serbatoi, vengono prima sabbiati e poi rivestiti con polveri epossidiche con ottima resistenza alla corrosione in terreni difficili e agli urti meccanici».
La temperatura è un elemento fondamentale nel ciclo di verniciatura dei serbatoi interrati, dove il film di rivestimento deve avere uno spessore maggiore per garantire prestazioni anticorrosive e meccaniche. Per ottenere uno spessore di 500 μm e raggiungere la reticolazione della vernice con una sola mano di verniciatura a polvere epossidica verde, i serbatoi devono essere preriscaldati a una temperatura compresa tra 130-140°C. I serbatoi fuori terra sono protetti dalla corrosione mediante una doppia mano di fondo epossipoliestere, seguita da una finitura poliestere bianca certificata Qualicoat Classe 1.
Il primer epossipoliestere è formulato per essere molto versatile sia per la ritenzione del calore durante l’indurimento che per la sovraverniciatura, mentre la finitura poliestere aiuta a mantenere brillantezza e colore, anche in condizioni climatiche avverse.
MIGLIORAMENTO DELLA PROTEZIONE E DELLE PRESTAZIONI AMBIENTALI
I serbatoi fuori terra sono protetti in modo ottimale dalle intemperie da un sistema a due mani composto da un primer epossipoliestere PPG zinc free, seguito da una finitura poliestere bianca certificata Qualicoat Classe 1.
Per proteggere i serbatoi interrati viene applicata una sola mano di verniciatura a polvere epossidica verde PPG con uno spessore di 500 μm per elevare le prestazioni anticorrosione.
Oggi la Antonio Merloni Pressure Vessels produce più di 40.000 serbatoi all’anno, dei quali 30.000 sono ora rivestiti con vernici in polvere PPG.