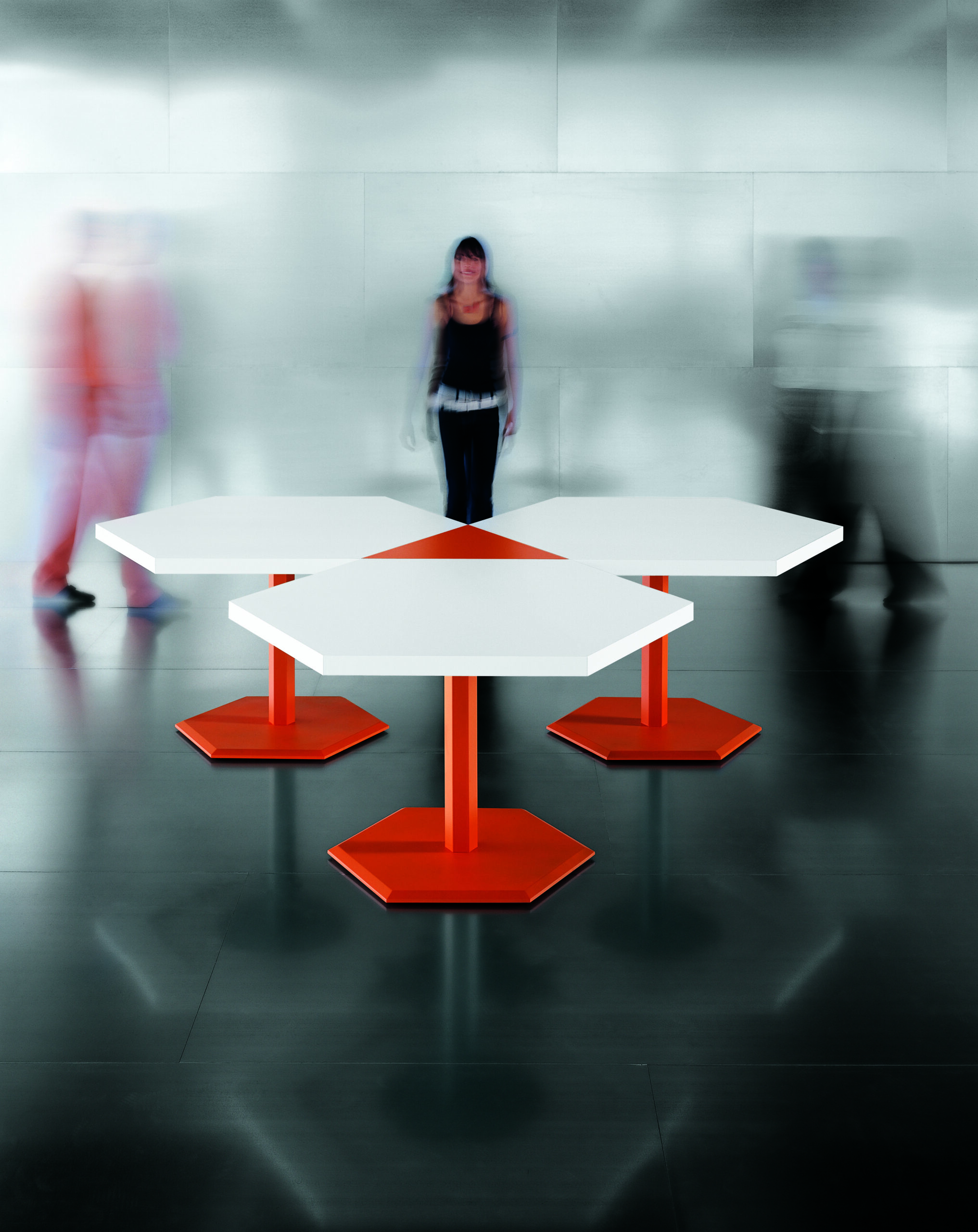
NEI MERCATI OLTREOCEANO LA VERNICIATURA A POLVERI DELL’MDF RIMANE UNA TECNOLOGIA DI GRANDE
La verniciatura a polveri di MDF è una tecnologia ben conosciuta che, nonostante un certo sforzo promozionale e qualche importante investimento compiuto negli anni – in particolare tra i 15 e i 10 anni fa – ha infine avuto una scarsa diffusione, in particolare nei mercati principali per la verniciatura del legno e derivati (Italia e Spagna, per esempio).
Alcune aziende e alcuni tecnici hanno insistito sullo sviluppo delle relative tecnologie, in alcuni Paesi europei (Italia, Belgio, Cechia) e extraeuropei (Messico).
In Messico, Homero ed Erick Treviño hanno sviluppato esperienze e conoscenze tecniche particolarmente avanzate. Li abbiamo recentemente incontrati e abbiamo fatto un punto della situazione riguardo la tecnologia.
Erick Treviño: «Da più di dieci anni siamo impegnati nello sviluppo dell’applicazione di polveri su supporti di MDF. Abbiamo prodotto e verniciato decine di migliaia di m2 di MDF verniciato a polveri, ricercando nel frattempo vernici e sistemi d’applicazione e polimerizzazione adeguati. Oggi siamo in grado d’offrire sia il servizio, sia la tecnologia completa per chi intende verniciare supporti di MDF con sistemi a polveri. Non sottolineo qui i vantaggi della verniciatura a polveri dell’MDF, sono già piuttosto conosciuti. Non vorrei neppure soffermarmi sull’analisi dei principali problemi, sono anch’essi conosciuti. In questi anni di produzione abbiamo potuto ben valutare i primi e affrontare i secondi, con successo di mercato. Oggi mettiamo a disposizione del mercato americano tutto il know-how che abbiamo sviluppato industrializzando il processo».
Homero Treviño: «Veniamo dalla produzione di vernici in polvere (l’azienda è oggi parte del gruppo PPG Messico, ndr), e ci siamo focalizzati sulla selezione dei prodotti in polvere che riteniamo diano, attualmente, il migliore risultato. Si tratta di prodotti sviluppati e prodotti da un piccolo gruppo d’aziende (abbiamo effettuato una selezione che copre ogni possibile mercato, non solo nelle Americhe), tutti con caratteristiche di reattività, facilità d’applicazione e resistenze molto interessanti e che consentono i migliori risultati, in combinazione con il sistema d’applicazione e polimerizzazione IR che abbiamo messo a punto. Il responsabile di una di queste linee di prodotti ritiene che, rispetto ai cicli a liquido, quelli a polveri per MDF:
- sono molto più resistenti all’acqua
- sono 6 volte più veloci rispetto a un ciclo a liquido tipico (le polveri si applicano in mano unica sulle 3 dimensioni, mentre un ciclo tipico a liquido richiede fino a 7 fasi d’applicazione successive)
- costano, per pezzo verniciato, un 30% in meno rispetto a un ciclo tipico a liquido
- consumano un 50% di energia in meno
- i costi della sola applicazione, inclusi quelli di manutenzione, si riducono fino all’80%
- non emettono VOC e richiedono procedure autorizzative significativamente più semplici.
Concordiamo con lui. Il ciclo prevede di appendere i pannelli di MDF su appositi telai, dunque in verticale, l’applicazione su supporto preriscaldato mediante forno IR (a gas), sviluppato insieme a un nostro partner di origine statunitense (Titan Catalytic) e la successiva cottura, sempre utilizzando la tecnologia IR in forno sviluppato con il nostro partner.
Oggi conosciamo le necessarie regolazioni dell’emissione IR, il posizionamento ottimale dei pannelli radianti e sappiamo come dimensionare dei forni. Anche per la fase d’applicazione, che avviene automaticamente in cabina di verniciatura in materiale dielettrico, abbiamo sviluppato un contro-elettrodo che consente di evitare sia i sovraspessori sui bordi, sia l’effetto “cornice”, l’eccesso di polvere depositata nelle aree vicine al bordo, che ne inficiano l’estetica».
Erick Treviño: «Il contro-elettrodo scarica le polveri al superamento del profilo del pezzo in fase di verniciatura, che quindi non si depositano in eccesso nella faccia posteriore dei pannelli e sui loro bordi. Il bordo è da sempre una fase critica del processo. In dipendenza dal tipo di MDF utilizzato e dalla sua lavorazione (in particolare, contenuto d’umidità e precisione di taglio del pantografo), può essere necessario “sigillare” il bordo con un impregnante all’acqua, applicato a spruzzo, perfettamente riverniciabile con le polveri (anche in questo caso, prodotto da un nostro partner). Se si escludono questi casi particolari, di norma la fase d’applicazione con contro-elettrodo permette di affrontare e risolvere con successo il problema bordi senza la necessità di quest’ulteriore applicazione.
Tra l’altro, anche rispetto alle finiture con laminati o melammina la verniciatura a polveri dell’MDF offre un vantaggio significativo: si effettua in una sola fase sull’intero substrato, invece dei rivestimenti con laminati o melammina, che richiedono processi (d’incollaggio) multifase, per le due facce del supporto, bordi e modanature».
Homero Treviño: «L’applicazione si effettua in una cabina in materiale dielettrico per il cambio rapido del colore. Anche in questo caso abbiamo sviluppato la macchina in collaborazione con un partner specializzato (l’italiana Sef Italia).
I reciprocatori sono installati in successione nei due lati della cabina; davanti alle pistole, come detto, sono operativi i contro-elettrodi. Il sistema “tipo” prevede l’interconnessione tra le diverse fasi di processo mediante semplice trasportatore monorotaia. Riteniamo che l’opzione di un sistema birotaia (P&F), che pure mettiamo a disposizione, non sia la soluzione economicamente ottimale, ai fini dell’ottenimento dei risultati desiderati, e dev’essere giustificata da altri motivi (logistica e programmazione della produzione, per esempio).
In definitiva, siamo convinti di poter offrire alle aziende interessate all’uso dell’MDF, insieme ai nostri partner, la migliore tecnologia per poter immediatamente rendere operativo il processo di verniciatura a polveri di questo tipo di supporto.
Ci occupiamo direttamente della progettazione, installazione e avviamento dell’impianto, del processo e della formazione del personale incaricato. Infine: mettiamo a disposizione del mercato il know-how che abbiamo sviluppato in questi oltre 10 anni d’industrializzazione del processo, con il supporto dei fornitori di sistemi e prodotti che ci hanno accompagnato in questa difficile ma soddisfacente sfida tecnologica».
Molto interessante
Questo articolo lo trovo molto interessante,spero susciti interesse anche da parte di chi,nel nostro paese potrebbe riprendere seriamente in considerazione lo sfruttamento di tale tecnologia.A differenza di quanto descritto,il nostro sistema,brevettato in coppia con il Sig. Soli della Ditta STS,prevedeva un Primer per consentire elettrostaticità sul supporto e la penetrazione della polvere ,sino a 60/90 Micron e garantire il perfetto ancoraggio , anche in casi lavorazioni di Sublimazione a 200 gradi per 30 minuti come da collaudi effetuati anche dai nostri fornitori del tempo , come Dupont , e Jotun Norvegia…..Ma è passato molto tempo. Sarei interessato a conoscere eventuali sviluppi.Saluti.