Autore: La Redazione
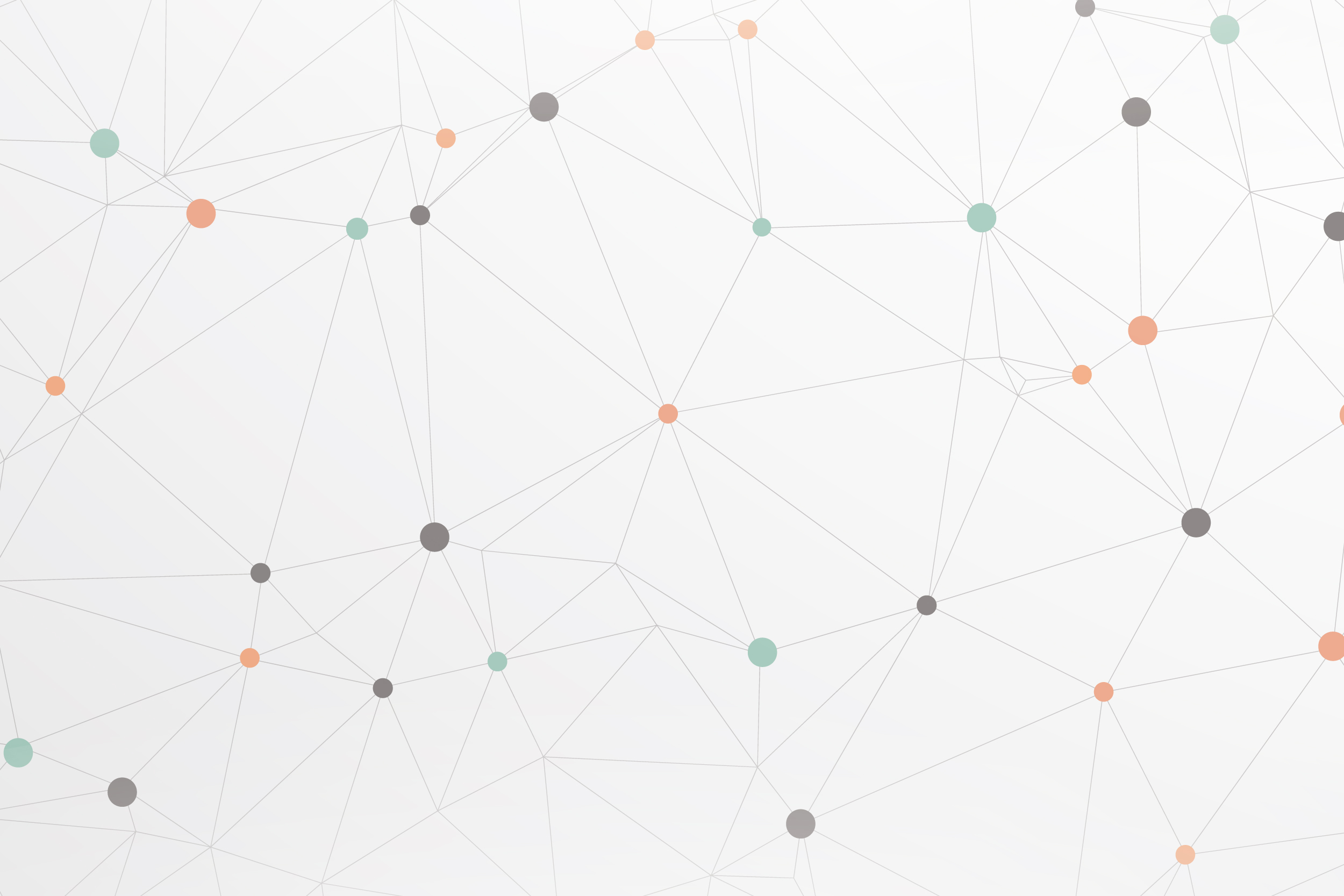
Il consueto appuntamento con le nanotecnologie di pretrattamento, che tradizionalmente la Rivista del Colore – Anver organizza annualmente in collaborazione con il Politecnico di Milano nella celebre aula Natta del dipartimento di chimica dell’ateneo milanese, non si è lasciato sopraffare dagli eventi recenti e, quest’anno si è svolto in modalità agile sottoforma di webinar.
A inaugurare l’evento i docenti del Politecnico Paolo Gronchi, per l’introduzione della problematica legata all’industrializzazione dei composti carboniosi sp2 e Massimiliano Bestetti, presentando un breve resoconto delle attività di ricerca sulle nanotecnologie nel periodo 2000 – 2020.
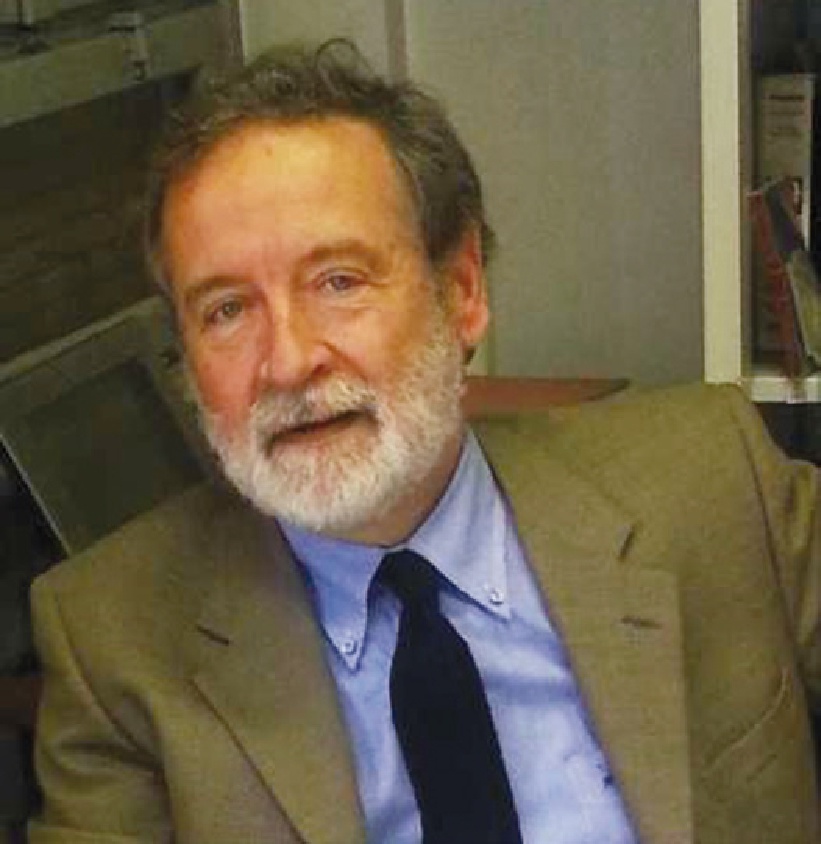
Paolo Gronchi apre il pomeriggio di aggiornamento introducendo i composti carboniosi, la cui industrializzazione oggi è limitata, basandosi su tesi e prove condotte col gruppo Italcementi, interessato a questi elementi in quanto in grado di impartire caratteristiche interessanti ai prodotti vernicianti quali l’aumento delle proprietà meccaniche o conduttive dei materiali su cui vengono applicati.
I grafeni formati dagli stessi elementi del carbonio (di cui è allotropo), ma con una base cristallina differente e molti suoi simili con carboni ibridizzati sp2, sono infatti potenziali cariche di dimensioni nanometriche che possono migliorare notevolmente le prestazioni di materiali a base di polimero/legante, sia organico che inorganico, con un carico estremamente basso. Oggi abbiamo a disposizione dei materiali compositi (come le vernici) a base di grafene, nanotubi di carbonio, grafene nanoplatelets (GNP – più difficilmente compatibili con altri materiali come leganti, polimeri ecc) e grafene ossido (GO – più facilmente compatibili), i più utilizzati.
I composti di grafene si possono ottenere con diversi metodi ma i più diffusi sono l’esfoliazione meccanica (secca) e l’esfoliazione in fase liquida. Tra i due principali problemi legati all’industrializzazione di questo tipo di prodotti vi è in primo luogo l’agglomerazione delle particelle dei prodotti grafenici che tendono ad aggregarsi nella matrice polimerica, mantenendo le proprietà del composto ben al di sotto del potenziale previsto. Esistono dei disperdenti (tipo il glicerolo) per ovviare a questo problema ma non sono ancora soddisfacenti al 100%.
L’altra principale problematica dell’utilizzo industriale dei prodotti vernicianti a base grafene è invece collegata a una preparazione di base molto lunga (2 o 3 giorni).
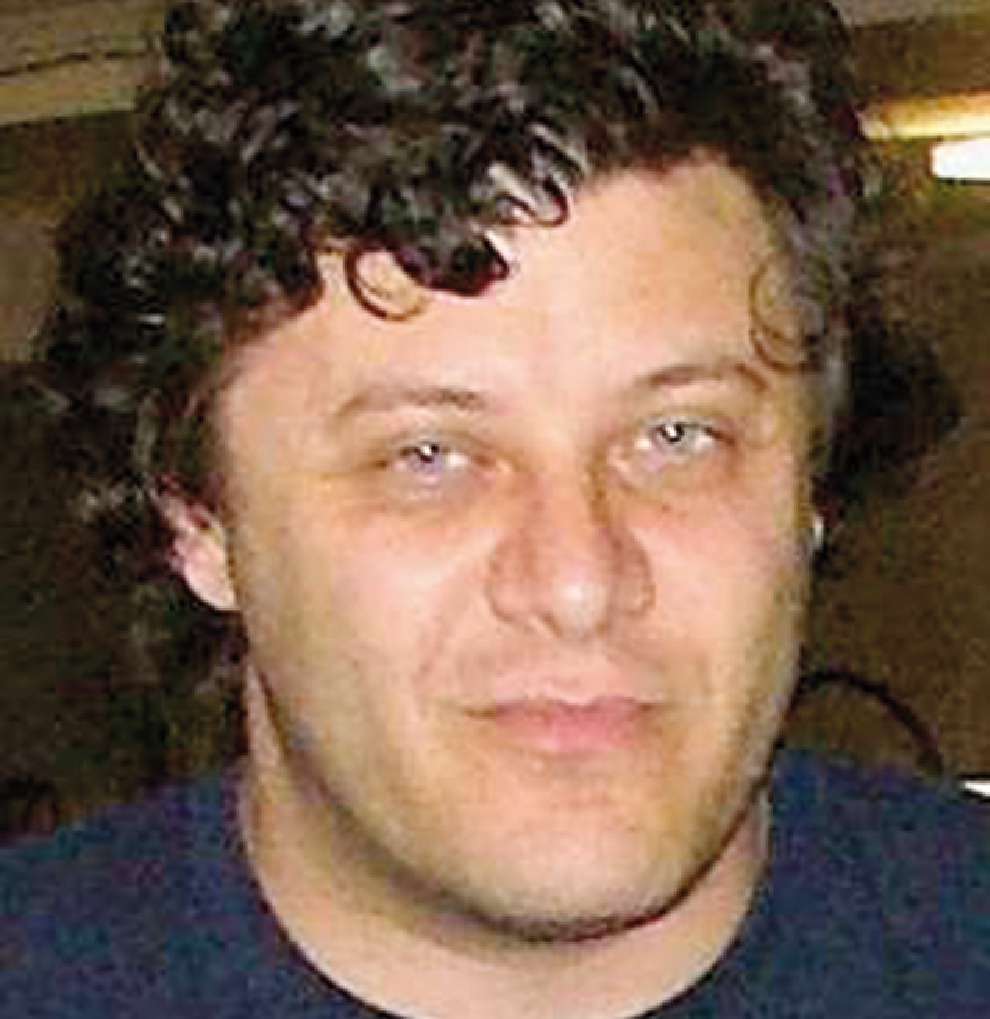
A seguire e in conclusione della sessione istituzionale del pomeriggio, Massimiliano Bestetti riassume l’importante percorso di ricerca degli ultimi 20 anni sui nanotubi di carbonio.
La prima volta che appare il nome di questi elementi è su una rivista russa “Giornale di chimica e fisica” nel 1952, in cui appaiono anche le prime immagini dei nanotubi osservati con il microscopio elettronico a trasmissione: multiparete e con un diametro di 50 nm. Tuttavia, ancora non si parlava di nanotecnologie. La primissima ricerca sui nanotubi di carbonio risale alla decade 2000-2010 e verte sull’immagazzinamento dell’idrogeno, vettore energetico molto importante ma difficile da confinare e trasportare nei nanotubi, ottimi immagazzinatori. I limiti gravimetrici e volumetrici della quantità di idrogeno immagazzinato in un serbatoio (almeno 6,5 % in peso e almeno 62 kg/ m3) stabiliti dall’automotive, hanno regolato tutte le successive ricerche, con risultati disomogenei. Massimiliano Bestetti e altri ricercatori del Politecnico di Milano, attraverso la tecnica elettrochimica, ottengono uno 0,3 %, lontano quindi dai parametri richiesti. Essendo i nanotubi una immensa famiglia di strutture, ciò che li distingue è la difettosità, le impurezze e perciò disporre di un unico campione è pressoché impossibile: da qui la grande varietà di risultati.
Un’altra importante ricerca tenta invece di fare crescere i nanotubi di carbonio all’interno dell’allumina anodica monoporosa, realizzando due strutture: un ossido anodico ordinato (cioè che cresce in maniera autorganizzata e di cui l’allumina è archetipo) e la crescita dei filamenti dei nanotubi all’interno dei pori.
Dopo svariate ricerche, nel 2002, al convegno Nanotecnologie, viene presentata una rassegna sull’uso dei nanotubi all’interno dei rivestimenti metallici, per arrivare nel 2004 a sostenere che i nanotubi di carbonio all’interno dei rivestimenti metallici, ne migliorano effettivamente il coefficiente di attrito, il comportamento all’usura e la microdurezza della matrice.
Dopo questi anni si verificano i primi tentativi di produzione dei nanotubi di carbonio multiparete secondo tre fasi: sintesi del catalizzatore, produzione dei nanotubi di carbonio tramite letto fluido CVD (dai cui nasce una polvere di nanotubi), purificazione (da ferro e alluminio) e funzionalizzazione. Un lavoro da cui nasce un primo brevetto sul catalizzatore (come si prepara un catalizzatore ferro su allumina) e alla costruzione del primo reattore con cui uno studente effettua le prime prove buone di sintesi dei nanotubi di carbonio, costituito da un tubo di quarzo all’interno del quale fluisce dal basso la miscela etilene/idrogeno/ azoto.
Dal 2010 Massimiliano Bestetti in collaborazione con diversi professionisti prosegue il lavoro di ricerca sui nanotubi di carbonio, che porta a diversi risultati molto importanti tra cui: la costruzione del primo vero reattore industriale per la preparazione del catalizzatore e dei nanotubi di carbonio (5 tonnellate al giorno), la loro purificazione e il mantenimento della funzionalizzazione; l’immagazzinamento dell’energia tramite dei super-immagazzinatori, con particolare dedizione allo studio degli elettrodi a base di nanotubi di carbonio per creare dei super condensatori; i tentativi di commercializzazione dei nanotubi di carbonio in diversi campi industriali (2015); e infine l’attività svolta con l’azienda Verniciature Bresciane, di sperimentazione dell’uso di reti metalliche ricoperte dalla peluria dei nanotubi per separare l’olio dall’acqua, creare dei fluidi termovettori, vernici conduttive per anti taccheggio, schermi della radiazione elettromagnetica, tessuti riscaldati elettricamente e altre attività. Il risultato è un brevetto sui piani cottura riscaldati elettricamente con una vernice a base di nanotubi e un secondo sulla vernice da utilizzare per riscaldare quei piani cottura.
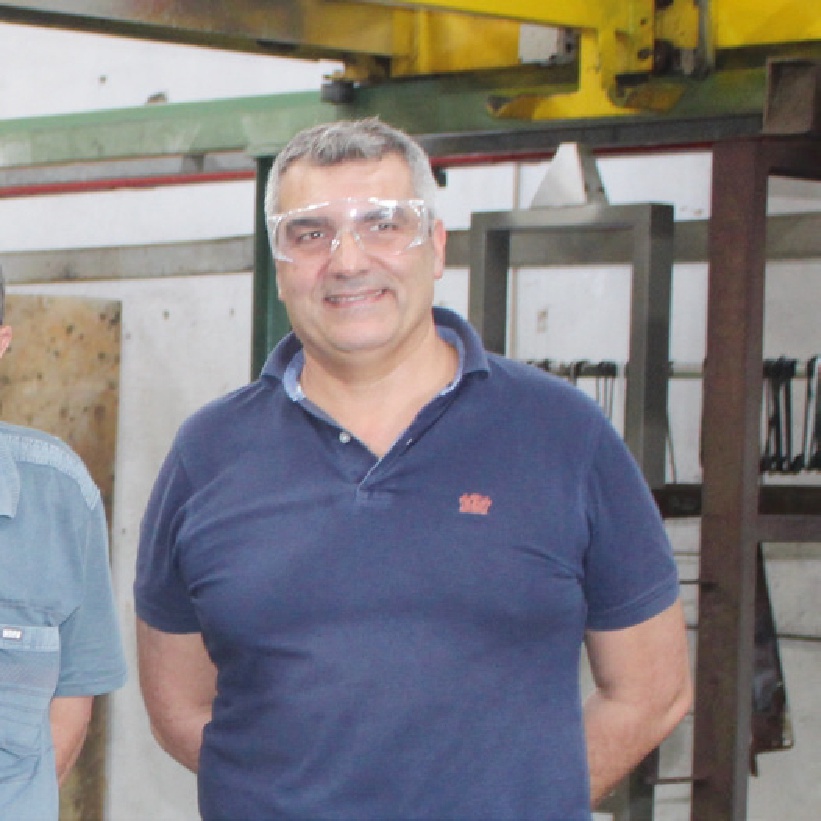
Vincenzo Carcò responsabile della divisione general industry di Chemetall Italia, società chimica che produce soluzioni per il pretrattamento delle superfici metalliche, presenta una nuova tecnologia di rivestimento lanciata circa 2 anni fa: un unico prodotto che adempie contemporaneamente alle funzioni di pretrattamento e di fondo protettivo. Si tratta di un rivestimento organico che lavora su acciaio laminato a caldo e a freddo, su ghisa e su materiali ad alta resistenza, attualmente disponibile solo in nero (RAL 005) e grigio chiaro, che garantisce omogeneità e spessori uniformi.
La soluzione presenta agenti chimici, leganti, acceleranti e promotori di adesione. In una prima fase, l’agglomerazione, si ha un piccolo dissolvimento di ioni metallici (che reagiscono col prodotto e creano un deposito di film organico) dalla superfice metallica, uno sviluppo di idrogeno e quindi un deposito di ossidi metallici. In una seconda fase, aggregazione, il film organico si deposita sulla superficie metallica.
Il prodotto, che ha una resistenza di 720 ore alla prova di nebbia salina con ossidazione al taglio inferiore ai 2 mm e di 1008 ore con ossidazione al taglio inferiore ai 4 mm, è in grado di raggiungere omogeneamente gli spigoli vivi del manufatto, garantendo uno spessore uniforme anche nelle parti interne (al contrario di quanto accade con la cataforesi).
Il film è molto più elastico quindi tutti i test condotti relativamente alle resistenze meccaniche sono stati passati eccellentemente. Questa tecnologia ha un contenuto di VOC molto basso, comparabile alle moderne cataforesi, è approvato reach ed è compatibile con qualunque tipo di vernice (liquida o in polvere) e può essere sovraverniciato. Il ciclo standard di applicazione prevede: sgrassaggio alcalino, risciacquo con acqua di rete e demineralizzata, verniciatura, risciacquo con acqua demi e cottura.
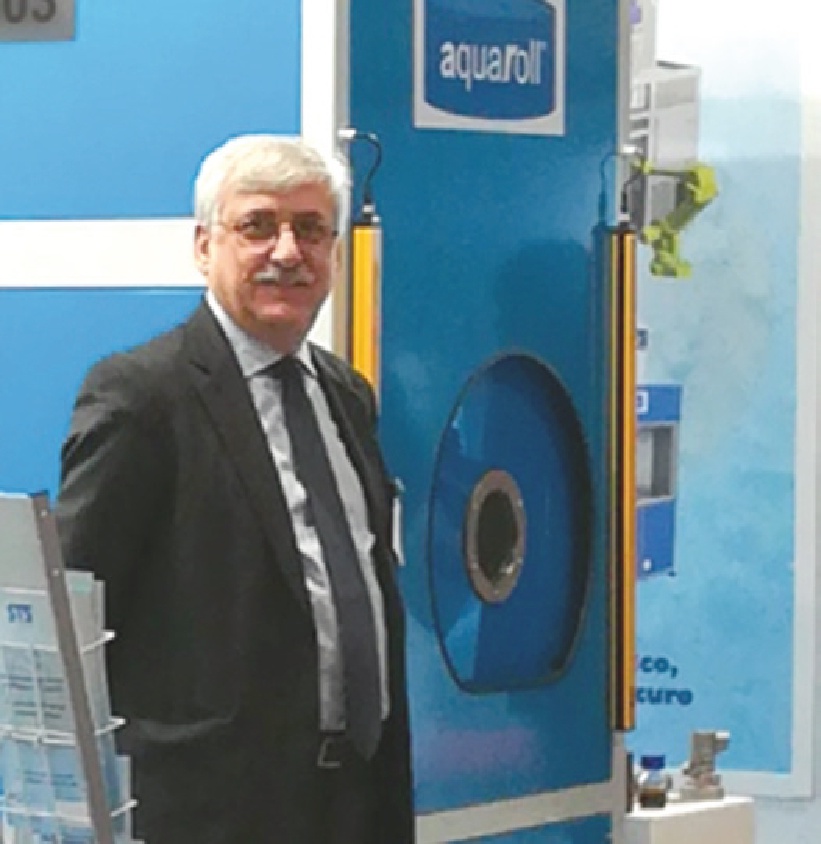
Ciro Poggioli, titolare della STS azienda romagnola impegnata da vent’anni nel settore del lavaggio industriale e del trattamento delle superfici, presenta un prodotto nanotecnologico per la pulizia dei manufatti prima della verniciatura. Rollclean è una soluzione acquosa sostenibile concepita per sgrassare superfici in metallo ferroso e non ferroso (acciaio, rame, ottone, alluminio). L’utilizzo di questo prodotto nanotecnologico è vantaggioso per diversi aspetti:
- Efficacia: ha un altissimo potere detergente, rimuove grassi e oli da tutte le superfici, è facile da risciacquare e non lascia residui, ha un potere antiossidante, è un degno sostituto dei solventi;
- Versatilità: è ideale per l’impiego in impianti concepiti e sviluppati dall’azienda stessa ma opera egregiamente anche su impianti esistenti di lavaggio a ultrasuoni, a spruzzo o ad agitazione pneumatica;
- Sicurezza: il prodotto è atossico e ininfiammabile, non produce esalazioni e vapori pericolosi, ha un pH contenuto e una scheda di sicurezza con tossicità, infiammabilità e reattività pari a 0 oltre a essere di semplice smaltimento, privo di emissioni COV, totalmente idrosolubile e privo di fosfati;
- Economicità: Rollclean non emulsiona, non evapora, non si degrada col calore e prolunga la sua durata.
Rollclean è stato sviluppato con l’intenzione di eliminare i fosfati utilizzando come detergenti i sali di bicarbonato di sodio e sostituendo i tensioattivi con una serie di polimeri solubili in acqua, che creano una barriera tra il supporto da sgrassare e la soluzione sgrassante, che agisce in continuo. Nei detergenti tradizionali questa funzione la ricopre il tensioattivo, che ha tuttavia una natura emulsionante che non evita del tutto la rideposizione del contaminante sulla superficie. Al contrario succede coi prodotti di sgrassaggio nanotecnologico, la cui natura non emulsionante agisce da anti depositante.
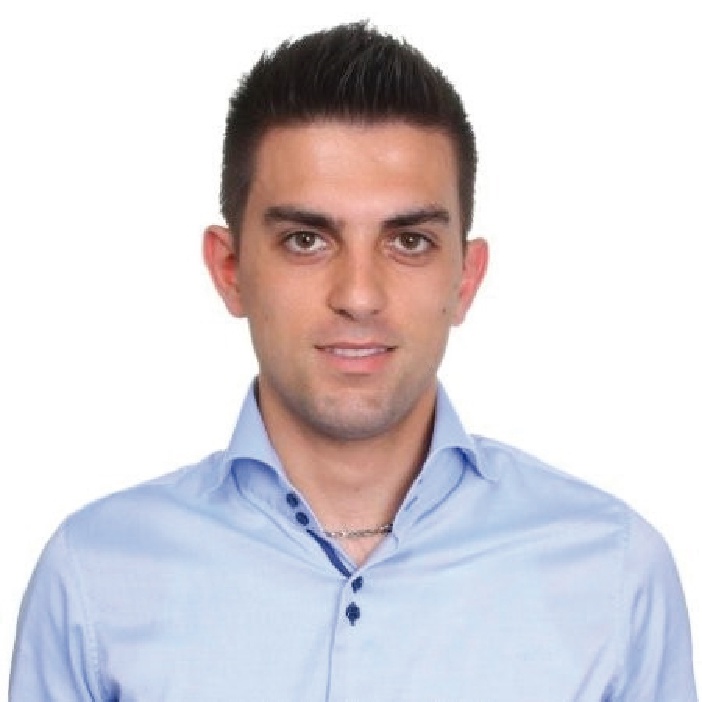
Andrea Monti di Chemetall presenta l’ultima acquisizione nanotecnologica in materia di pretrattamento: l’Oxilan, evoluzione della tradizionale fosfatazione tricationica allo zinco che permette di lavorare con uno spessore nanotecnologico (da 50 a 100 nanometri fino a 250 per le conversioni più spinte), creando una struttura amorfa.
È una tecnologia ibrida con sali clorurati di zirconio che si vanno a depositare sul substrato, coadiuvati da alcuni polimeri a base silanica in grado di ricoprire la superficie generando una maggior protezione dalla corrosione ed elevata affinità con la vernice e garantendo elevate prestazioni meccaniche. È una tecnologia molto agile perché permette di accorciare notevolmente le linee di processo: anche i risciacqui e la passivazione possono essere omessi, generando una riduzione dei consumi di energia e acqua e dei costi di manutenzione.
È una tecnologia green perché non contiene metalli pesanti come nichel, boro e cromo ed è completamente esente da fosfati. Ciò permette l’implementazione nelle aree in cui sono stringenti le norme per lo scarico dei reflui. In fase applicativa Oxilan genera una quantità di fanghi trascurabile, di due ordini di grandezza inferiori ai processi tradizionali. Il bagno è facilmente controllabile tramite pHmetro, conduttimetro e qualche controllo da laboratorio. È una tecnologia che funziona a temperatura ambiente e consente quindi un risparmio notevole di CO2.
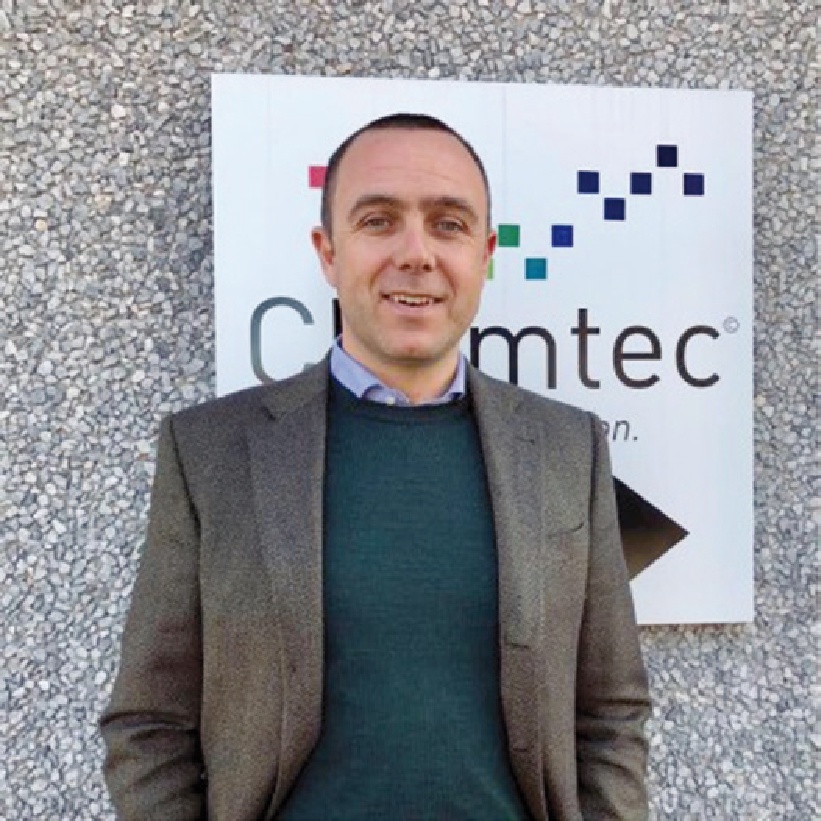
Carlo Guidetti, titolare di Chemtec, azienda milanese che produce sistemi di pretrattamento monostadio a freddo, sistemi di detergenza industriale di stampo tradizionale, processi chimici e impianti per il trattamento delle acque reflue e delle acque chiare, svernicianti ecologici, presenta un nuovo sistema nanotecnologico basato sui composti organici del fosforo, che si propone come alternativa alla fosfatazione tricationica. Unico ad oggi, questo sistema, rispetto alle altre nanotecnologie, garantisce una qualità alta, costante e una semplicità estrema di utilizzo e di gestione.
Pronortec è un processo organico esente da metalli, si applica su superfici sgrassate, prive di ossidi e risciacquate e crea un rivestimento nanometrico uniforme formato da carbonio, fosforo e ossigeno con uno spessore di circa 50 nm. Si tratta di un rivestimento idrofobo (maggiormente resistente alla corrosione), reattivo (consente una maggiore adesione della vernice) e compatibile con vernice liquida, in polvere ed e-coat, che può essere applicato in normali tunnel di lavaggio (dopo sgrassaggio, disossidazione se necessario e risciacquo con acqua purificata), a immersione, per aspersione o nebulizzazione e non richiede risciacquo.
Pronortec è considerato anche un’alternativa vera ad altre nanotecnologie a base di zirconio, titanio o silani e garantisce risultati migliori, maggiore stabilità (il bagno dura all’infinito), non necessita risciacqui ed è semplicissimo da utilizzare. Può essere inoltre applicato come additivo nel risciacquo finale dopo fosfatazione tricationica/zinco.
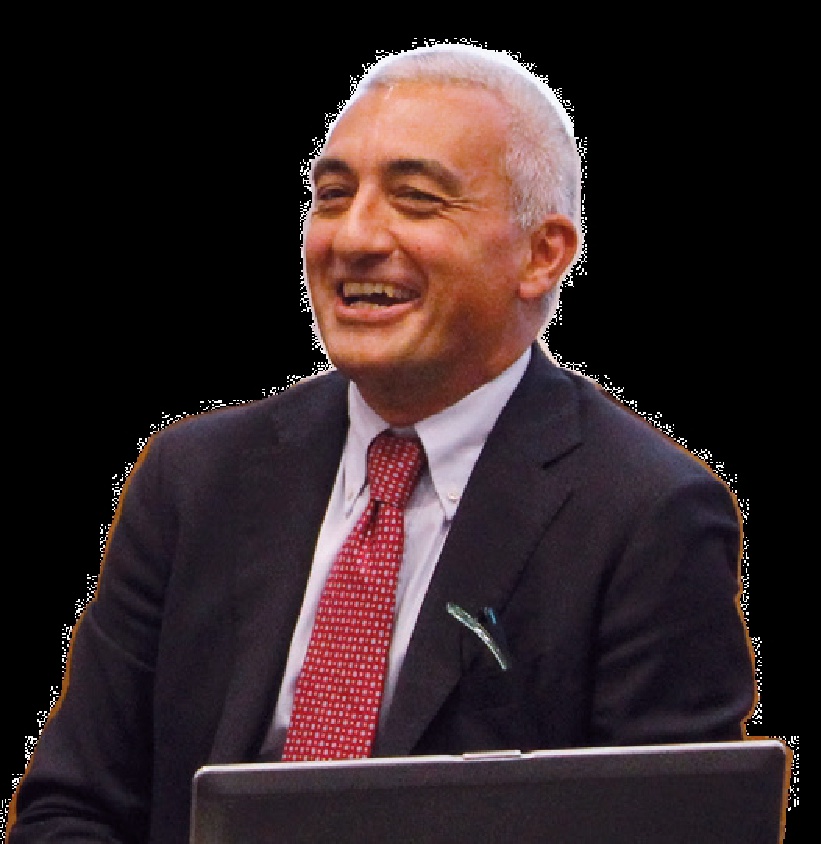
André Bernasconi di DN Chemicals, azienda specializzata nella produzione di prodotti per il trattamento delle superfici, delle acque reflue e di cabina e di prodotti di pretrattamento e sverniciatura, ha presentato i sistemi nanotecnologici di pretrattamento della linea Dollcoat SA. Flessibili e utilizzabili su impianti esistenti con piccole modifiche, questi prodotti si basano su oligomeri di sintesi ottenuti da silani, che funzionano da promotori di adesione e fanno da barriera alla corrosione. La linea Dollcoat SA si propone come alternativa o completamento dei processi tradizionali: all’interno di un fosfosgrassaggio o di uno sgrassaggio alcalino (fosfati di ferro o zinco), si può infatti aggiungere in finale un prodotto della linea Dollcoat applicato con nebulizzazione (ma non solo).
Gli impianti di nebulizzazione sono stati introdotti nel 2005 da Dollmar e hanno avuto successo in termini di riduzione dell’inquinamento. Sono composti da un semplice modulo esterno dove si produce la soluzione nanotecnologica che viene poi nebulizzata nella parte finale del tunnel. I pochi reflui vengono raccolti in una vaschetta, drenati e rimessi in circolo. In questo modo la soluzione nanotecnologica non verrà mai contaminata, la qualità e l’omogeneità del pretrattamento saranno sempre costanti e superiori a quelle dei processi standard.
La nebulizzazione ha inoltre il vantaggio di raggiungere anche parti nascoste dei manufatti, al contrario delle applicazioni tradizionali e il costo del processo è molto competitivo, considerando il risparmio in termini di operazioni di smaltimento (la linea Dollcoat SA infatti, non produce fanghi).
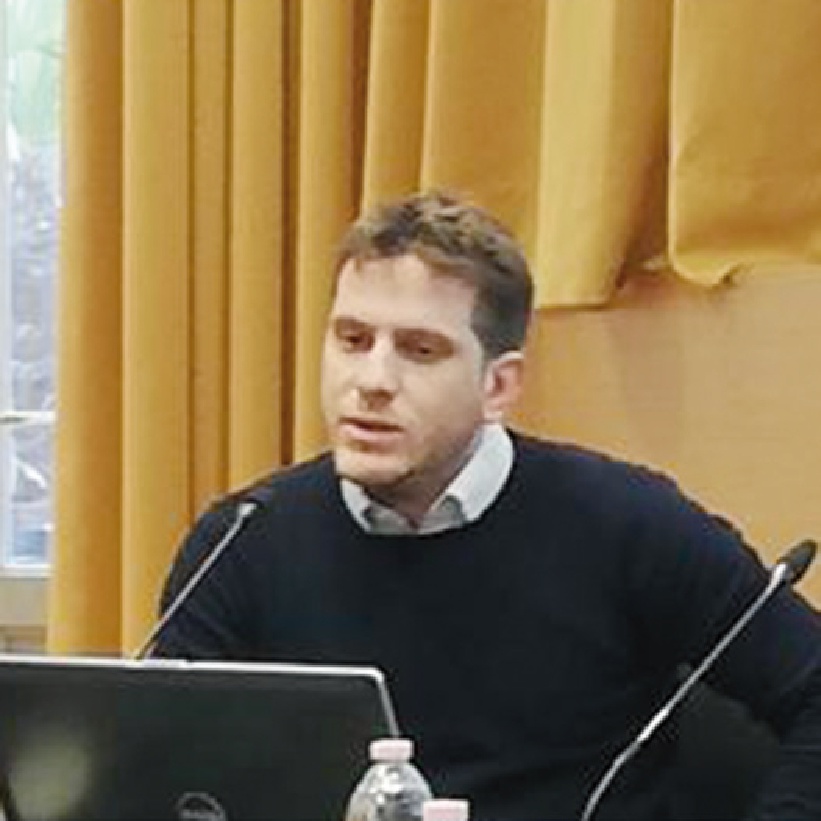
Daniele Briguglio, responsabile tecnico di laboratorio di DN Chemicals, interviene per approfondire chimicamente i composti che costituiscono la linea Dollcoat SA. Sono silossani le cui strutture si dividono in due grandi famiglie: una a “scalini” e una “a gabbia”, la più utilizzata. Queste strutture, in grado di incorporare ioni metallici, si ottengono principalmente attraverso due reazioni: idrolisi e condensazione in ambiente acido (che favorisce la reazione di idrolisi) e basico che invece favorisce la reazione di condensazione. Utilizzando parametri legati alla cinetica di reazione si possono ottenere diversi gradi di reticolazione del rivestimento che possiamo osservare (più è alto il grado, maggiore è il grado di protezione del substrato metallico che ricopre).
Dopo varie prove su varie formulazioni, è stato scelto il prodotto che meglio rispondeva a caratteristiche di resistenza alla corrosione e vi sono stati inseriti dei nanotubi di carbonio. Daniele Briguglio conferma quanto detto da Gronchi in merito all’ottenimento della ottimale dispersione di nanotubi all’interno della molecola, che, pur raggiunta, non garantisce una prestazione ottimale del sistema, il quale subisce una degradazione causata da un’eventuale esposizione della superficie metallica con l’elettrolita (prove condotte con metodo ACET). Questo è forse dato dalla modifica del nanotubo attraverso la sua funzionalizzazione perché ne modifica la struttura.
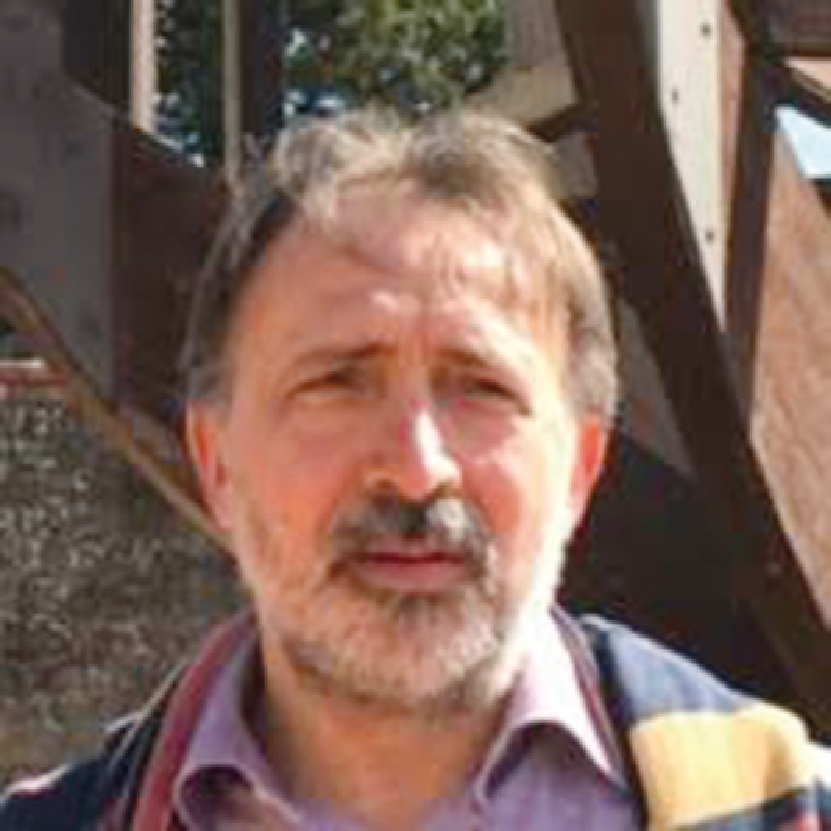
Pierluigi Cerioli della Henkel, di cui è responsabile dell’assistenza tecnica, chiude il pomeriggio di aggiornamento con la presentazione del processo nanotecnologico di autoforesi, sistema di cui l’azienda è stata pioniera. Con il prodotto utilizzato direttamente su metallo senza necessità di fosfatazione o conversione chimica intermedia, si vanno a raggiungere meglio gli spigoli e le parti interne delle strutture che, se non adeguatamente protette (come spesso accade con la cataforesi) dal film del rivestimento che viene applicato, possono usurarsi prima del tempo e perdere le funzioni per cui sono fabbricati, come ad esempio i radiatori o i sistemi automatici di rilevamento ed estinzione degli incendi.
Non solo, l’utilizzo del prodotto nanotecnologico di Henkel consente un’importante riduzione dei costi di processo annui pari al 29% (consumo di energia, di acqua, di prodotti chimici, di costi di smaltimento e molto altro).
Insomma, i processi di rivestimento di nuova generazione in sostituzione di fosfatazione allo zinco, al ferro e al fosfosgrassaggio, migliorano la resistenza alla corrosione, possono essere utilizzati su tutti i metalli, formano uno strato di conversione nanometrica e possono essere applicati a spruzzo, a immersione o APNR.
Inoltre questo sistema è semplice da applicare, è altamente flessibile e adattabile a vari processi/materiali, non necessita di un controllo del bagno in quanto la soluzione rimane sempre fresca, si può accendere e spegnere senza fermi produzione. I rivestimenti nanotecnologici autoforetici rappresentano una buona soluzione ai processi tradizionali.
Non necessitano di strati di conversione e in alcuni casi è sufficiente un’essiccazione a 90°C prima dell’applicazione del topcoat in polvere. In questo modo si accorcia la linea di produzione e si ottiene una protezione omogenea su tutto il pezzo, con una protezione eccellente del bordo, si elimina la formazione di morchie e si riducono i consumi energetici. Bonderite può anche essere utilizzato in un sistema a due mani che prevede l’applicazione di una mano di primer e successiva mano di polvere con polimerizzazione contemporanea (co-curing). Il sistema offre diversi vantaggi: semplificazione del processo con riduzione degli spazi, maggiore flessibilità, risparmio energetico, alte prestazioni.