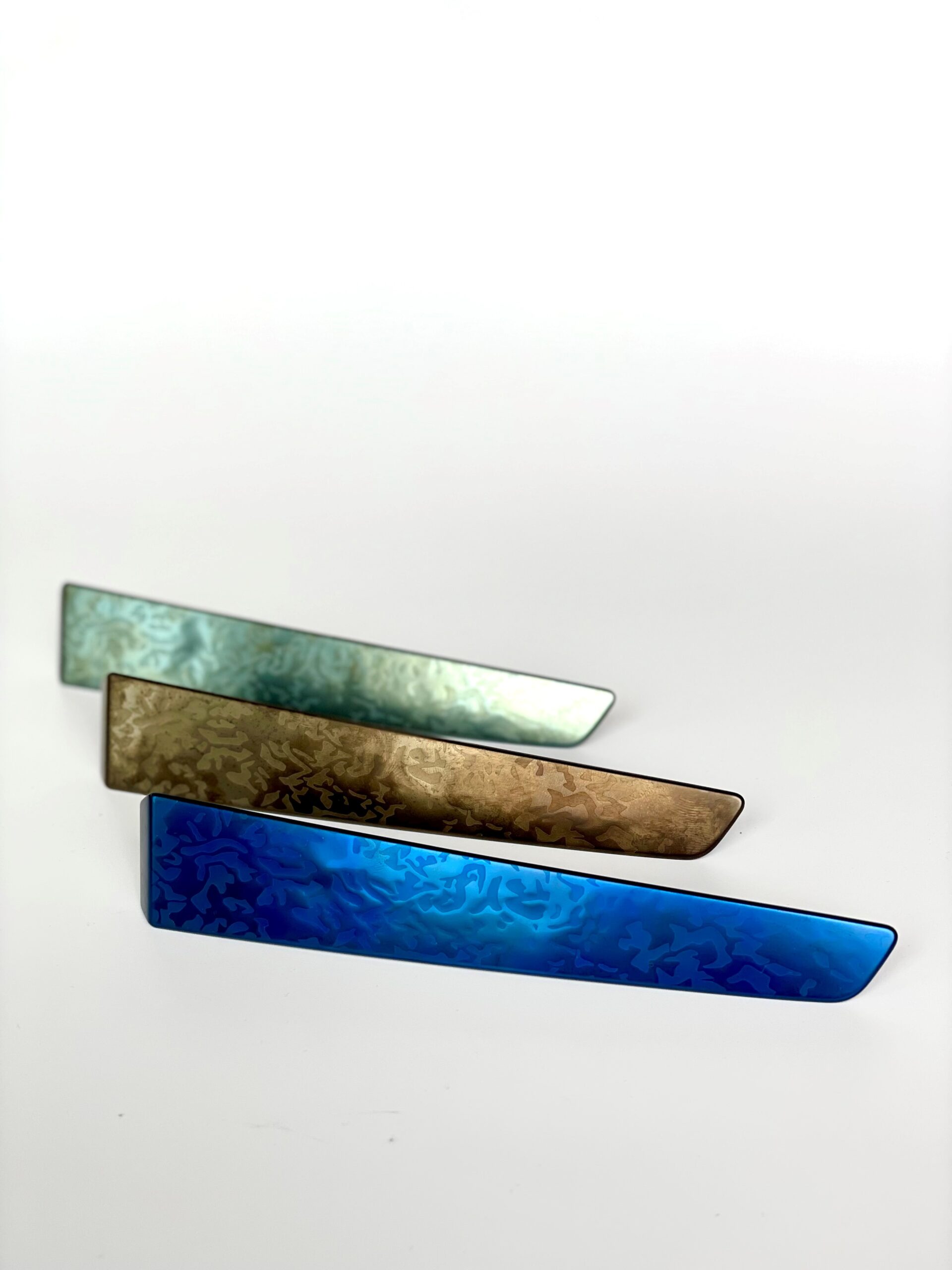
Appassionato tecnico dei processi PVD, l’autore mette in luce le potenzialità ancora inespresse di una tecnologia che offre molte soluzioni attuali e potenziali per ottenere finiture senza precedenti sotto il profilo della durabilità e della gamma estetica.
La Physical Vapour Deposition (tecnologia già conosciuta con l’acronimo PVD, deposizione fisica in fase vapore) è un processo ampiamente utilizzato in varie applicazioni industriali che prevedono la deposizione di rivestimenti protettivi e durevoli. Le attività legate alle tecnologie PVD raggiungeranno senza dubbio i miliardi di euro nei prossimi anni, vista la crescita delle capacità tecniche e produttive e l’offerta di prospettive multifunzionali di successo, già comprovate in molte applicazioni. Il mercato globale dei rivestimenti decorativi è stato valutato in 82 miliardi di dollari nel 2022 e si prevede che raggiungerà i 100 miliardi entro il 2030. Il PVD avrà una quota sostanziale di questo successo.
È interessante notare che di recente i processi PVD hanno guadagnato terreno nella finitura di articoli di moda di lusso per dare finiture protettive e decorative di alto livello estetico, a sottolineare l’allontanamento dal dominio dei processi galvanici tradizionali, tipicamente utilizzati in questo settore. I rivestimenti PVD hanno suscitato l’interesse di molte aziende e designer per la loro capacità unica di combinare perfettamente proprietà decorative e protettive. Questi rivestimenti offrono vari colori e finiture, rendendoli versatili per le diverse necessità dell’industrial design. Inoltre, la durata dei rivestimenti PVD garantisce che gli articoli del luxury fashion mantengano il loro fascino estetico per periodi più lunghi rispetto a quanto possibile con i metodi tradizionali.
Si prevede che il mercato dei rivestimenti PVD decorativi crescerà costantemente nel prossimo decennio. L’aumento della domanda di superfici di alto livello estetico in campi come l’architettura, l’automobile e dei beni di consumo ne favorirà ulteriormente la crescita. Le normative ambientali incentivano sempre più le opzioni di rivestimento a minor impatto ambientale. Il progresso tecnologico, come dimostrato negli anni passati, migliorerà senz’altro anche durabilità e prestazioni estetiche dei rivestimenti PVD.
Ci si aspetta che il mercato dei rivestimenti decorativi PVD registrino una crescita significativa già nei prossimi cinque anni. La loro crescente adozione in campo automotive, elettronica e dei beni di lusso alimenterà tale l’espansione. Le proprietà superiori delle superfici trattate con PVD, come la resistenza all’usura e il basso impatto ambientale, faranno aumentare la sua quota di mercato. I progressi della tecnologia PVD permettono di ampliare sempre più le opzioni disponibili di colore ed effetti, e di ottenere una efficienze di processo via via superiori. Con consumatori di fascia alta, si prevede che il Nord America, l’India e l’Europa saranno i mercati più significativi per le finiture in PVD, tuttavia anche la regione Asia-Pacifico sarà un’area di crescita chiave, grazie ai suoi alti tassi di sviluppo industriale.
Le principali tecnologie di deposizione fisica in vapore [per sublimazione, essendo allo stato solido i materiali “vaporizzati”, ndr] sono le seguenti:
- Evaporazione termica: Il materiale viene riscaldato per sublimare e condensare sul substrato.
- Sputtering: gli ioni bombardano un bersaglio (metallico), che espelle atomi, i quali si depositano in successione sul substrato.
- Evaporazione con fascio di elettroni: un fascio di elettroni focalizzato riscalda e fa sublimare il materiale di partenza.
- Deposizione laser pulsata: un laser ad alta potenza fa sublimare il materiale di un bersaglio, che poi si deposita sul substrato.
- Deposizione a vapore ad arco catodico: un arco elettrico fa sublimare il materiale da una sorgente catodica.
Di questi metodi, la deposizione ad arco catodico (CVA) e lo sputtering sono i più utilizzati nelle applicazioni PVD decorative. Nella tecnologia ad arco catodico, si utilizza un flusso supersonico di plasma completamente ionizzato derivante dall’arco in continuo movimento (casuale o diretto). A seconda del materiale del catodo e della presenza di gas di processo, questo metodo può produrre film di metallo, ceramica o carbonio (simile al diamante).
Lo sputtering consiste nel sublimare (vaporizzare) un materiale solido bombardandolo con energia ionica. È ampiamente utilizzato per formare film sottili su oggetti 2D o 3D. L’High Power Impulse Magnetron Sputtering (HiPIMS) è un progresso relativamente recente nella tecnologia dello sputtering, utilizzato per la deposizione fisica di rivestimenti di film sottili (nanometrici), basato sul magnetron sputtering, una sorgente di energia pulsata ad alta tensione. Nell’HiPIMS, una scarica di energia ad altissima tensione e di breve durata viene focalizzata sul materiale da sublimare. In questo modo si crea un plasma ad alta densità che ionizza fortemente il materiale di rivestimento. Si tenga conto, inoltre, che lo sputtering può essere utilizzato anche su materiali catodici non conduttivi, mentre l’arco catodico può essere utilizzato solo su catodi conduttivi.
Gli archi catodici sono precedenti all’HiPIMS e sono stati ampiamente utilizzati nell’industria. Tuttavia, l’High Power Impulse Magnetron Sputtering (HiPIMS) ha recentemente guadagnato attenzione come tecnologia PVD emergente perché, come affermato da Andre Anders, un professore di ricerca esperto di PVD, l’HiPIMS combina le parti migliori del magnetron sputtering con altri metodi energetici di deposizione di rivestimenti, come la placcatura ionica (Ion Plating) e la deposizione al plasma ad arco catodico. La famosa “rassegna di Anders” ha messo a confronto gli archi catodici e l’HiPIMS (Andre Anders, 2014, Surface and Coatings Technology vol. 257 p. 308). Considerando che lo sputtering può funzionare con catodi non conduttivi, l’HiPIMS consente di operare in modalità mista, in cui si formano spot catodici a vita breve nella pista magnetica che producono una ionizzazione potenziata di sputtering sul bersaglio nella transizione controllata (glow-to-arc) nello sputtering, per la deposizione ad alta velocità di film di carbonio, come dimostrato da David McKenzie e dal suo gruppo di ricerca a Sydney, Australia.
Colori: le loro varietà e i metodi di produzione
I rivestimenti PVD sono disponibili in vari colori, come oro, oro rosa, nero, grigio canna di fucile, bronzo, blu, arcobaleno, argento, champagne e rame. Questi colori sono ampiamente utilizzati in gioielleria, orologeria, componenti metallici per architettura e applicazioni industriali. Il loro aspetto varia in base allo specifico processo PVD e ai materiali utilizzati. Il controllo sempre più preciso dei processi PVD con finalità (anche) decorative più avanzate si misurano con la metrica CIELAB, cioè a dire i colori ottenuti sono ripetibili.
I nitruri metallici utilizzati nei rivestimenti PVD hanno colori diversi. Ad esempio, il nitruro di titanio (TiN) appare dorato, il nitruro di zirconio (ZrN) diventa oro chiaro e il nitruro di cromo (CrN) produce una tonalità diversa. Anche altri ossidi e nitruri presentano colori unici, sia in base alla pellicola combinata con altri strati che alle loro proprietà ottiche intrinseche. I colori vengono creati attraverso l’assorbimento della luce e gli effetti di interferenza. Il controllo dei parametri di processo appropriati determinano le lunghezze d’onda della luce riflessa o assorbita [dello stesso autore, si veda anche quanto pubblicato, a proposito del controllo del colore e tecnologia HiPIMS in Verniciatura Industriale – Industrial Coating n. 666/2023, ndr].
Sostituzione del Cr (VI) con il PVD
Il futuro dei processi industriali richiede la sostituzione dei metodi elettrochimici ad alto rischio, in particolare quelli che utilizzano il Cr(VI) e i bagni galvanici con cianuro, che l’Unione Europea ha limitato. Anche per questo stiamo assistendo a uno spostamento significativo verso l’utilizzo di rivestimenti ottenuti via PVD. Il processo elettrochimico detiene ancora una quota sostanziale di mercato, che sta gradualmente diminuendo. In questo momento, la combinazione di entrambe le tecniche, PVD e galvanica, può offrire nuove caratteristiche estetiche, una gamma di colori più ampia e texture diverse, che rendono il PVD sempre più importante per le applicazioni dove prevale l’aspetto decorativo, per esempio nell’industria dell’alta moda.
I recenti progressi della tecnologia PVD, inoltre, hanno migliorato resistenza alla corrosione e durabilità dei rivestimenti ottenuti, rendendola la scelta preferita per le applicazioni in campo decorativo ad alte prestazioni. Le procedure di controllo della qualità, come la misurazione degli spessori e i test di adesione, garantiscono prestazioni coerenti e affidabili del rivestimento ottenuto. Permangono, va segnalato, alcuni limiti per quanto riguarda l’uniformità del rivestimento su pezzi di geometria complessa, e la necessità di attrezzature specializzate per applicazioni specifiche.
I rivestimenti decorativi ottenuti per PVD sono applicati sia su substrati metallici che polimerici, vetro, carta, film plastici, rivestimenti interni per auto e tessuti. In alcune di queste applicazioni i rivestimenti colorati ottenuti via sputtering o HiPIMS hanno già una quota di mercato interessante. Tuttavia, dato l’uso diffuso dei substrati metallici in numerosi settori industriali, una parte significativa della ricerca è rivolta ai rivestimenti PVD su tali substrati. In ogni caso, i rivestimenti per substrati non metallici sono via via oggetto di maggiore attenzione. Ciò è particolarmente vero per i substrati polimerici tipici di componenti per esterno (e interno) nel campo dell’automotive.
Rivestimenti per automotive ottenuti via PVD
L’industria dei componenti polimerici nel settore automotive sta tornando in fermento, ci si aspettano cambiamenti significativi, anche per l’ingresso del veicolo elettrico (EV), che richiede leggerezza per compensare il peso delle batterie, e un nuovo design. Potenzialmente le tecnologie PVD potrebbero lavorare in linea con i tipici sistemi di rivestimento della carrozzeria, ma gli intervalli delle temperature dei processi di verniciatura (120-160 °C) costituiscono un limite per molti dei polimeri termoplastici, solo alcuni materiali termoindurenti potrebbero essere rivestiti in linea. Dunque, gli sviluppi dei rivestimenti di tali materiali via PVD si effettua, di norma a batch oppure in linee separate.
Tra i principali termoplastici utilizzati nel campo automotive citiamo l’ABS (acrilonitrile-butadiene-stirene), il policarbonato (PC), la poliolefina termoplastica (TPO), la poliammide (PA), il polimetilmetacrilato (PMMA) e il polibutilentereftalato (PBT); termoindurenti, il poliuretano rinforzato per reazione in stampo (PUR-RRIM), il composito in lastra stampaggio in lastra (SMC).
Con questi materiali si ottengono paraurti, cruscotti, lenti dei fari, specchietti retrovisori, parafanghi, mostrine e molto altro. Come si vede, applicazioni dove spesso il colore decorativo è necessario, e le finiture decorative ottenute con processi PVD sempre più interessanti.
In ambito automotive la tecnologia HiPIMS è già piuttosto utilizzata per applicare rivestimenti decorativi di colore grigio (antracite), a basse temperature.
Ganesan et al. hanno studiato la sintesi di carbonio amorfo altamente tetraedrico utilizzando questo metodo (R. Ganesan et al., 2015, J. Phys. D: Appl. Phys. vol. 48, 442001). Il loro studio ha rilevato che le differenze ottiche dei film di carbonio amorfo senza idrogeno dipendono della pressione e della tensione di polarizzazione costante applicata all’attrezzatura rotante su cui sono fissati i pezzi.
In uno studio successivo, Tucker et al. hanno anche misurato le variazioni ottiche rispetto alla tensione di polarizzazione applicata al substrato a pressione costante, (Journal of Appl. Phys. 2016 vol.119, 155303).
Infine, Ganesian et al. hanno individuato una ancora più ampia gamma di applicazioni e proprietà dei rivestimenti di carbonio amorfo duro, regolando la lunghezza dell’impulso nell’HiPIMS bipolare per avere un’elevata velocità di deposizione di film di carbonio amorfo liscio e duro (R Ganesan et al., 2023, Surface and Coatings Technology, vol. 454, 129199). Per ottenere il cosiddetto piano-black, la superficie deve essere morbida e completamente assorbente, dal punto di vista ottico. La lunghezza dell’impulso nell’HiPIMS bipolare è regolabile e quindi può essere ottimizzata per ottenere l’aspetto desiderato.
Colori decorativi PVD per rubinetteria di lusso
I produttori di rubinetti offrono spesso un’ampia gamma di opzioni di colori ed effetti ottenuti con sistemi PVD per migliorare l’aspetto e la durata dei loro prodotti. Il PVD è un processo di finitura specializzato che crea un rivestimento duro e resistente ai graffi sulle superfici metalliche. Ecco alcune popolari opzioni di colori ed effetti PVD disponibili nell’industria della rubinetteria tramite sputtering e arco:
- oro spazzolato: una finitura dorata calda e invitante con delicate pennellate per una sottile lucentezza
- oro lucido: una finitura oro lucida e riflettente per un aspetto lussuoso
- ottone spazzolato: una finitura ricca e profonda in ottone con una texture spazzolata per un fascino senza tempo
- nero opaco: un’elegante e moderna finitura nera con una superficie liscia e non riflettente.
- grigio canna di fucile: una sofisticata finitura metallica scura che ricorda le armi da fuoco
- oro rosa: una finitura rosa-oro elegante e di tendenza per un tocco di glamour
- nickel spazzolato: una finitura in nichel classica e versatile, con una texture spazzolata che conferisce una morbida luminosità
- bronzo oliato: una finitura in bronzo caldo e anticato con sottili sfumature di rame per un fascino vintage
- bronzo champagne: una morbida e calda finitura in bronzo con accenni di champagne per un look elegante e raffinato
- ottone satinato: finitura in ottone liscia e discreta, con una morbida lucentezza satinata per un fascino sofisticato.
Questi colori ed effetti consentono varie opzioni all’industrial designer per adattarsi agli stili di bagno e cucina. Le finiture PVD sono note per la loro durata, la resistenza all’appannamento e la facilità di manutenzione rispetto ai metodi di placcatura tradizionali.
Rivestimenti a tecnologia ibrida
È stato sviluppato un rivestimento unico di colore blu e rosso rosato per articoli di lusso, utilizzando una combinazione di deposizione a strato atomico (ALD) e tecnologia PVD. La tecnologia ALD consente di ottenere una varietà di nuovi colori grazie all’interferenza, mentre la combinazione del colore di base PVD e il controllo dello spessore del film ALD permettono di ottenere un’ampia gamma di colori ed effetti ripetibili e uniformi che completano il design dell’articolo. Questo processo di rivestimento avanzato migliora l’appeal visivo degli articoli di lusso e offre una protezione superiore contro l’usura e la corrosione. Il controllo preciso del colore e della durata rende i rivestimenti a tecnologia ibrida la scelta migliore per i prodotti di fascia alta in vari settori. Gli strati ALD vengono applicati su un substrato colorato, offrendo varie opzioni decorative.
La combinazione di PVD e ALD garantisce la perfetta conformità della deposizione, anche su parti di forma complessa. Questa combinazione offre un’eccellente protezione per i substrati soggetti a corrosione. Ad esempio, la combinazione PVD-ALD protegge l’ottone dalla corrosione e l’argento dall’appannamento. Questa tecnologia avanzata consente anche di creare disegni unici e intricati che migliorano l’estetica dei prodotti.
La possibilità di applicare più strati di materiali diversi garantisce che il rivestimento sia visivamente accattivante e altamente durevole. Nel complesso, l’utilizzo di PVD e ALD nei rivestimenti a tecnologia ibrida offre una protezione senza precedenti e opzioni di personalizzazione per vari prodotti di fascia alta in diversi settori.
Rivestimenti PVD idrofobici e oleofobici
I rivestimenti PVD sono utilizzati in varie applicazioni, tra cui la prevenzione o la riduzione delle impronte digitali e delle macchie sulle superfici frequentemente toccate dalle dita umane, come smartphone, tablet, computer portatili, occhiali e lenti. Le impronte digitali sono costituite da componenti oleosi e acquosi che aderiscono alla superficie, creando segni antiestetici e difficili da pulire. I rivestimenti oleofobici/idrofobici resistono alle impronte digitali e sono resistenti all’acqua.
Oltre a essere antiestetiche, le impronte digitali possono compromettere le prestazioni dei dispositivi otticamente sensibili e dei touchscreen, riducendone la chiarezza e la sensibilità. Per ottenere le proprietà anti-impronta, i rivestimenti PVD sono combinati con rivestimenti nanoparticellati, formando uno strato sottile e trasparente sopra lo strato PVD. I rivestimenti nanoparticellati a base di PVD sono costituiti da materiali a bassa energia superficiale e con un elevato angolo di contatto, il che significa che respingono le molecole d’acqua e d’olio e ne impediscono la diffusione sulla superficie.
Di conseguenza, l’aggiunta di nanoparticelle ai rivestimenti PVD riduce l’adesione e la visibilità delle impronte digitali, rendendole più facili da rimuovere senza lasciare residui.
Conclusioni
I rivestimenti PVD offrono molti vantaggi significativi nel migliorare le proprietà superficiali di un’ampia gamma di materiali rispetto ad altre applicazioni. Sono altamente raccomandati perché mostrano un’eccellente resistenza all’usura, forniscono protezione contro la corrosione e hanno una maggiore durezza. La tecnologia PVD consente di produrre un’ampia gamma di composizioni e spessori di rivestimento grazie alla sua versatilità, che permette di creare una grande varietà di effetti e colori. Gli investimenti inziali oggi possono essere considerati elevati; tuttavia, i benefici che si ottengono a lungo termine compensano ampiamente le spese. Grazie al continuo sviluppo della tecnologia, si prevede che il numero di applicazioni dei rivestimenti PVD aumenterà in diversi settori.
Rispetto alle tecniche di placcatura convenzionali, i rivestimenti ottenuti da PVD decorativo offrono vantaggi in termini di durata, possibilità di colore e rispetto dell’ambiente. Questi strati sottili e omogenei contribuiscono al loro fascino visivo, offrendo al contempo un’eccezionale resistenza all’usura e alla corrosione. Con il progredire della tecnologia, si prevede che i rivestimenti PVD saranno sempre più utilizzati in vari settori per scopi funzionali e ornamentali. Considerando i progressi delle capacità tecniche e produttive, le applicazioni versatili e il successo dimostrato in molti settori, il PVD non è più una tecnica senza più nulla da dire, al contrario, risponde a requisiti scientifici e industriali avanzati.
Ringrazio per l’ articolo alquanto interessante.
Chiedo se nell’ ambito di questo processo risulti necessario un processo di filtrazione oppure movimentazione dei liquidi