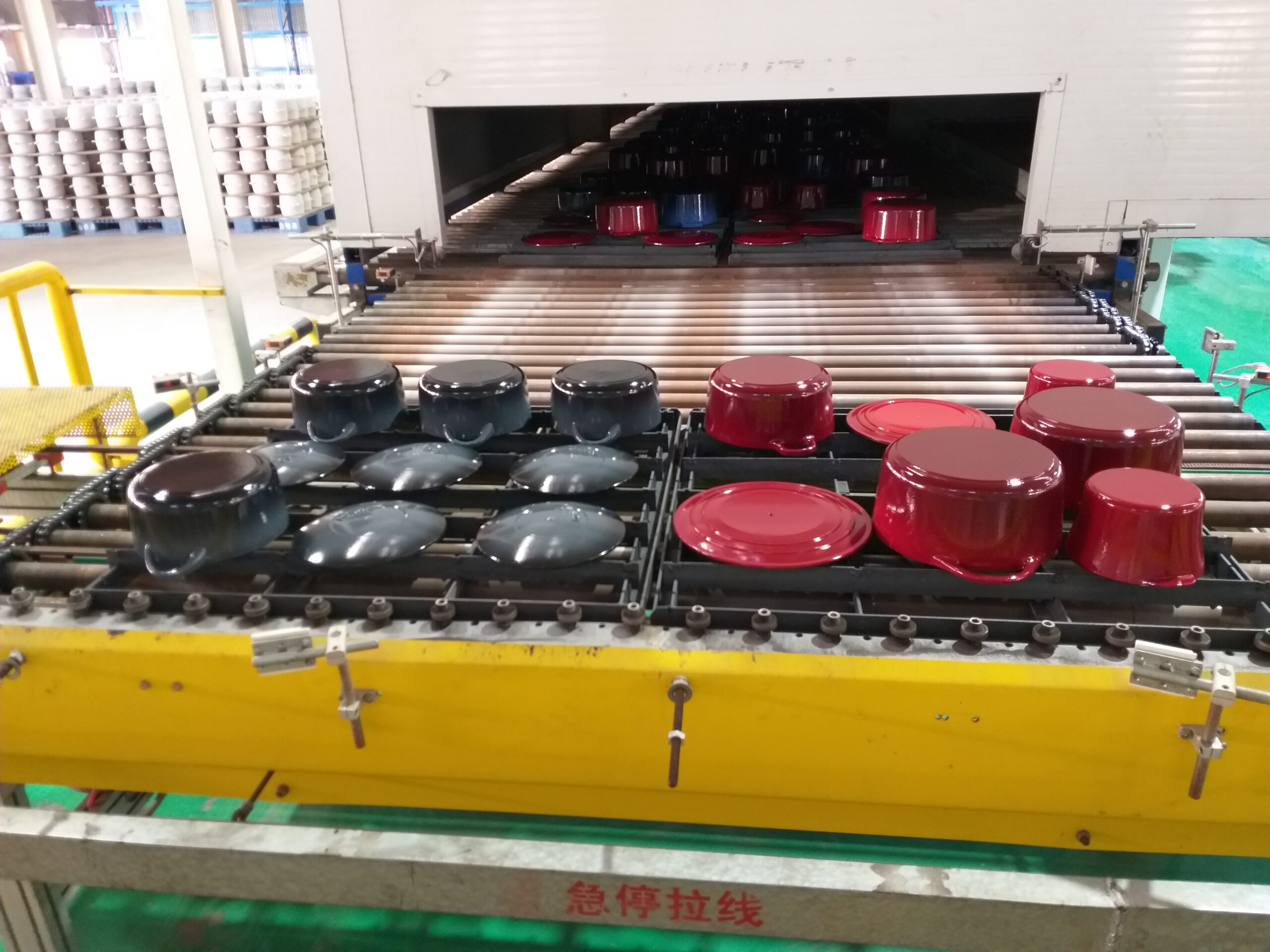
CONOSCIUTO FIN DALL’ANTICHITà, LO SMALTO PORCELLANATO È UN RIVESTIMENTO VETROSO CHE VIENE APPLICATO ALLE SUPERFICI MEDIANTE FUSIONE AD ALTA TEMPERATURA. VIENE UTILIZZATO IN MOLTI SETTORI, DALLE STUFE AI CASALINGHI, DALL’ARREDO URBANO AGLI SCAMBIATORI DI CALORE. Dal leader tecnologico internazionale nel campo dell’impiantistica per lo smalto porcellanato, una descrizione della tecnologia.
Durante i P&E Milano Coating Days dello scorso ottobre, Paolo Colombo di Trasmetal ha illustrato in dettaglio il processo di rivestimento delle superfici tramite smalto porcellanato. L’azienda è ai vertici mondiali per l’impiantistica dedicata a questa tecnologia. Lo smalto porcellanato, utilizzato fin dall’antichità, è uno strato vetroso che viene applicato ai materiali mediante fusione ad alta temperatura. La sua composizione è basata su miscele di silice, fondenti e pigmenti minerali.
Storia e prime applicazioni
Lo smalto porcellanato, conosciuto fin dall’antichità tanto quanto il vetro, è stato tradizionalmente impiegato per scopi decorativi. Esempi storici di tale utilizzo sono la Pala d’oro della Basilica di San Marco a Venezia e la Corona Ferrea custodita nel Duomo di Monza. Nel corso del tempo, le applicazioni dello smalto porcellanato si sono estese anche alla protezione di materiali ferrosi, come ghisa e acciaio, in ambito domestico e industriale.
Utilizzi attuali
In tempi recenti, lo smalto porcellanato ha trovato impiego anche su superfici meno soggette alla corrosione come acciaio inossidabile, alluminio e rame. Questo dimostra che, oltre a proteggere, questo materiale svolge anche una funzione decorativa. La norma UNI 8762 definisce lo smalto porcellanato “un prodotto vetrificato per rivestire superfici di metallo e vetro a scopo protettivo, funzionale e decorativo. Massa vetrosa solidificata ottenuta per fusione e brusco raffreddamento di componenti inorganici, fusa sul supporto a temperature comprese tra 450 e 950°C”.
Caratteristiche dello Smalto Porcellanato
Lo smalto porcellanato (che non è né un rivestimento ceramico, per la sua diversa composizione chimica, né una vernice in quanto materiale inorganico) è unico per il legame chimico che si sviluppa tra la matrice vetrosa e il substrato, grazie alla vetrificazione ad alta temperatura. Questo rivestimento inibisce l’attività organica e possiede diverse proprietà distintive dovute alla sua natura, tra cui:
- resistenza alla corrosione
- resistenza agli agenti chimici e atmosferici
- impermeabilità ai liquidi
- durezza e resistenza agli urti, graffi, abrasioni e usura
- incombustibilità e nessuna emissione di gas tossici in caso di incendio
- resistenza alle alte temperature e alle escursioni termiche (-50°C a +450°C)
- resistenza allo shock termico (oltre 300°C)
- conducibilità termica del composito supporto-smalto
- proprietà elettriche isolanti
- brillantezza e lucentezza superficiale
- stabilità dei colori
- igienicità e atossicità
- facilità di pulizia contro smog e graffiti
- inerzia chimica (non emette né assorbe odori o sapori)
Processo di smaltatura
Il ciclo di smaltatura comprende varie fasi: preparazione del supporto, applicazione a liquido o a polvere, essiccazione (nel caso di applicazione a liquido) e cottura.
La preparazione può includere sgrassaggio, sgrassaggio più decapaggio o granigliatura ma in alcuni casi è addirittura superflua.
L’applicazione a liquido avviene tramite spruzzatura, immersione, flow coat o elettroforesi, mentre l’applicazione a polvere si effettua tramite spruzzatura elettrostatica.
L’essiccazione (per applicazione a liquido) può avvenire elettricamente o tramite infrarossi a onda corta.
La fase di cottura è cruciale per garantire la fusione dello smalto e la sua completa reazione con il metallo, utilizzando forni intermittenti, a box, o continui con trasportatore aereo, rovescio, a rulli o a rete.
Applicazioni Tradizionali dello Smalto Porcellanato
Lo smalto porcellanato trova applicazione in diversi settori, tra cui:
- cucine e accessori: piani cottura, cavità di forni, griglie, spartifiamma, pentole in acciaio, ghisa e alluminio, barbecue
- sanitari e boiler
- elementi di arredo e industrial design
- stufe e tubi per fumisteria
- attrezzature chimiche, come reattori e serbatoi
- silos, vasche e cisterne
- lamiere per scambiatori Ljungström
- arredo urbano e segnaletica
- strutture ospedaliere e sale operatorie
- architettura ed edilizia: facciate, pannelli architettonici esterni e interni, gallerie e metropolitane.
Esempi di cicli di smaltatura e cottura
Un esempio tipico di linea di smaltatura a liquido è quella dedicata al trattamento dei boiler smaltati internamente. Il ciclo prevede pretrattamento a spruzzo, asciugatura, applicazione tramite flow coat, asciugatura dello smalto e cottura finale.
Altresì tipica è la linea di cottura delle pentole in ghisa, dotata di forni con resistenze a 800°C, seguiti da un tunnel di raffreddamento, per rendere le pentole manipolabili. In questo caso, e in generale per finalità più estetiche che protettive, i forni elettrici sono più indicati in quanto garantiscono una temperatura costante e l’integrità dei colori durante il processo.
In conclusione, lo smalto porcellanato rappresenta una soluzione versatile e duratura per la protezione e la decorazione di superfici in diversi settori industriali e domestici, grazie alle sue eccezionali proprietà fisiche e chimiche.
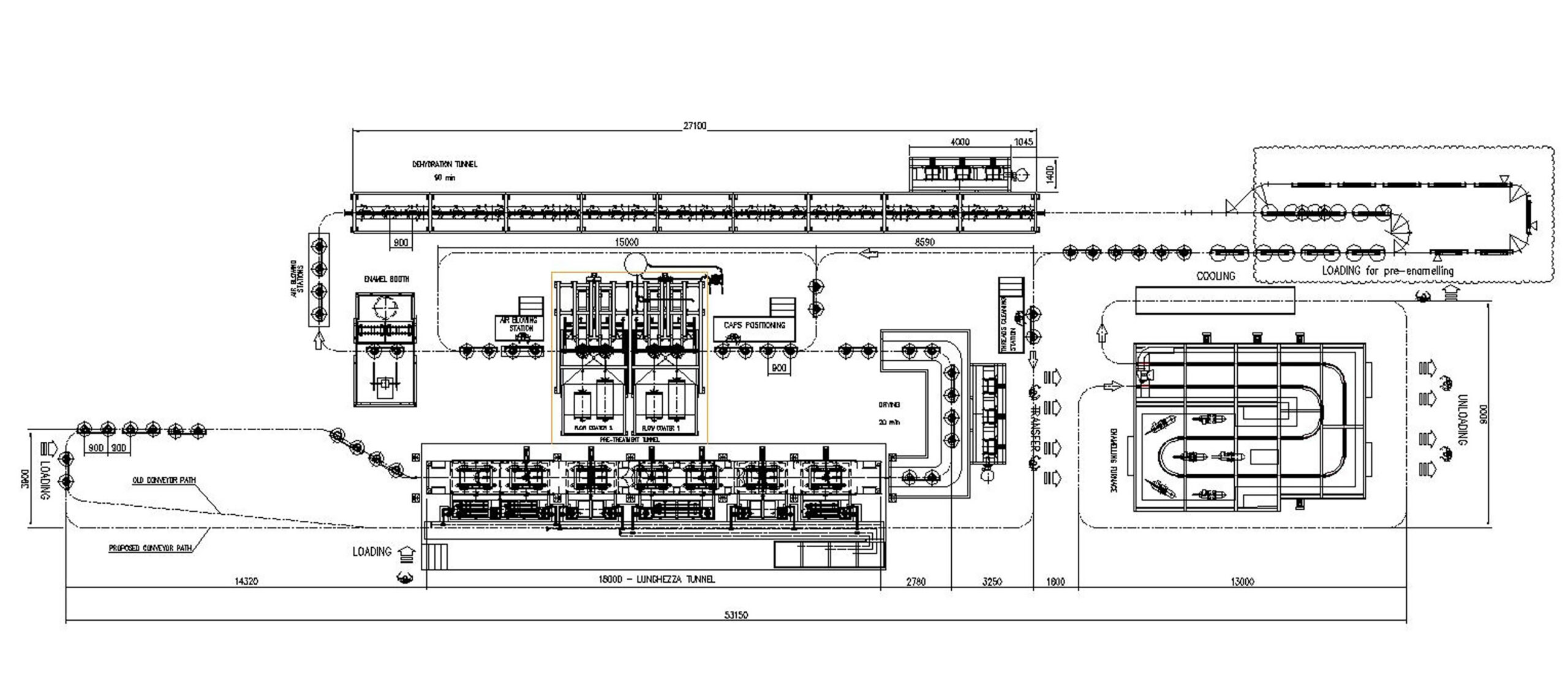
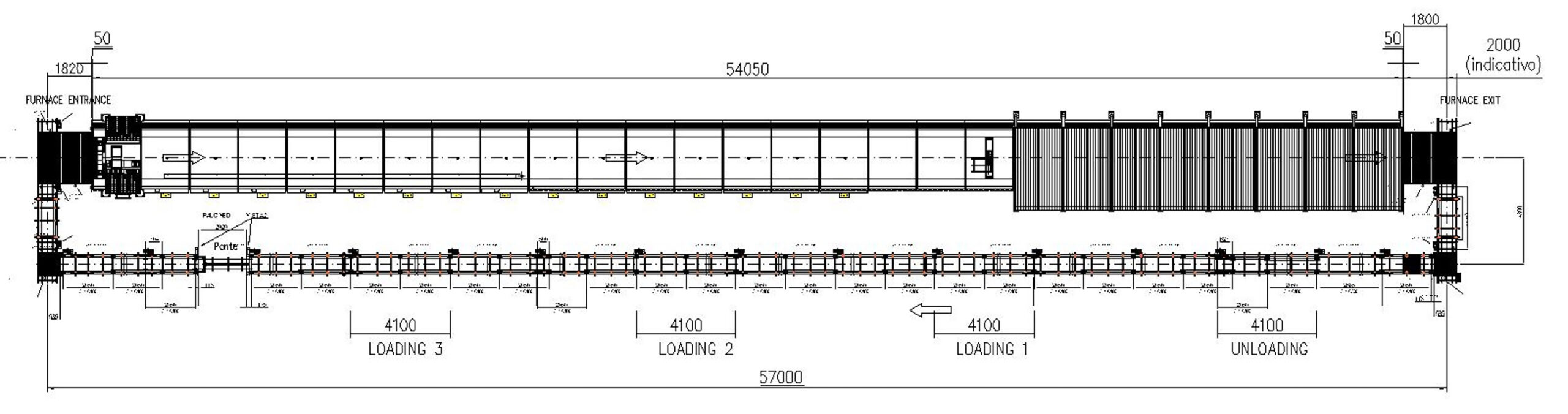