Intervista a: Simon Peter Bott, Forvia Hella
Cade uno degli argomenti che hanno rallentato negli anni passati la diffusione delle tecnologie pvd (deposizione fisica di metalli), la produzione discontinua. l’impianto visto e qui recensito lavora in linea ed è perfettamente integrato con i processi a monte e a valle dell’importante multinazionale dell’illuminazione del settore auto.
Grazie all’interessamento di Mara Arzuffi (Arzuffi PVD, Bernareggio, MB, Italia) e alla disponibilità di Simon Peter Bott, responsabile dei processi di rivestimento del gruppo Forvia Hella, abbiamo avuto l’opportunità di visitare uno dei grandi stabilimenti della multinazionale, nota per la produzione di sistemi d’illuminazione per il settore automobilistico, situato a Irapuato, in Messico.
La visita, finalizzata all’osservazione in azione di una linea industriale per la deposizione fisica di metalli su componenti per fari, ci ha permesso di accedere al grande reparto destinato ai trattamenti delle superfici dell’azienda: 3 linee d’applicazione di trasparenti UV con funzione antigraffio sulla faccia esposta dei fanali, 2 linee d’applicazione di prodotti antifog per la faccia interna dei fanali, 18 macchine a batch, alcune per metallizzazione termica, altre per processi PVD, oltre alla linea completamente automatica per processi PVD/rivestimento protettivo progettata, prodotta e installata da Arzuffi PVD.
«Alle linee tipiche per l’applicazione di prodotti speciali per fanali – ci dice Simon Peter Bott – si aggiungerà presto, in questo stabilimento, una nuova linea per lo stampaggio e la verniciatura dei radom, le fasce che nei veicoli elettrici sostituiscono il frontale copriradiatore. Questi elementi hanno funzioni protettive della sensoristica sempre più presente sui veicoli moderni: telecamere, radar, altri sensori per il supporto alla guida e alla futura guida autonoma. Si tratta di una sfida tecnologica importante, dato che le dimensioni e le forme dei pezzi sono molto superiori a quelle tipiche dei sistemi illuminanti e si richiedono alte resistenze e una qualità di finitura eccellente». [Si veda anche quanto pubblicato nell’esaustiva intervista rilasciata da Francesco Goi di Tecnofirma a questo proposito in VI n. 675-676/2024, pagg. 50 e seguenti o a questo link].
METALLIZZAZIONE E PVD. REPARTO A BATCH
«Concentrando l’attenzione sui sistemi per la deposizione di metalli sui componenti che stampiamo in questo stabilimento – ci dice Simon Peter Bott – abbiamo oggi 18 impianti che lavorano a batch con processi di evaporazione termica, PVD e misti. I processi d’evaporazione termica (metallizzazione sottovuoto) sono più semplici – ci dice Simon Peter Bott – ma una volta introdotti i sistemi PVD diventano chiari i loro limiti, la difficoltà a controllare esattamente gli spessori applicati e l’assenza di gamma del metallo evaporabile [tungsteno]. Con i processi PVD il controllo degli spessori applicati (e della loro omogeneità sulle superfici del pezzo) è invece fattibile, così come la gamma di materiali che si possono depositare, cosa che ci permette di rispondere alle richieste di differenziazione estetica dei pezzi metallizzati e, con la scelta dei metalli corretti da depositare, anche di aumentarne la durata (cromo, acciaio inox, rame, per esempio, anche se con una certa cautela relativamente alla scelta dei metalli, che possono subire variazioni di colore nel tempo)».
«Nell’ambito dei sistemi a batch, abbiamo lavorato con Arzuffi PVD per introdurre tutta una serie di miglioramenti volti a favorire capacità e facilità produttiva e produttività degli addetti, sviluppo delle “ricette” per tipo di rivestimento (controllando parametri tipici quali grado di vuoto, potenza e tempo di permanenza), uso di speciali porte girevoli per la camera, in modo da consentire scarico e carico dei pezzi durante l’operazione di deposizione dei metalli, progettazione di supporti specifici che permettano di evitare la mascheratura delle aree di superficie che non devono essere rivestite fuori linea. Gli impianti operanti in azienda sono in 3 configurazioni differenti, il che ci permette di rivestire tutti i componenti attualmente prodotti e provenienti da fornitori esterni. In tutti i casi, la capacità di ascolto, la flessibilità e la tempestività con cui vengono apportate le modifiche sono una delle caratteristiche che fanno di Arzuffi PVD uno dei nostri fornitori di riferimento».
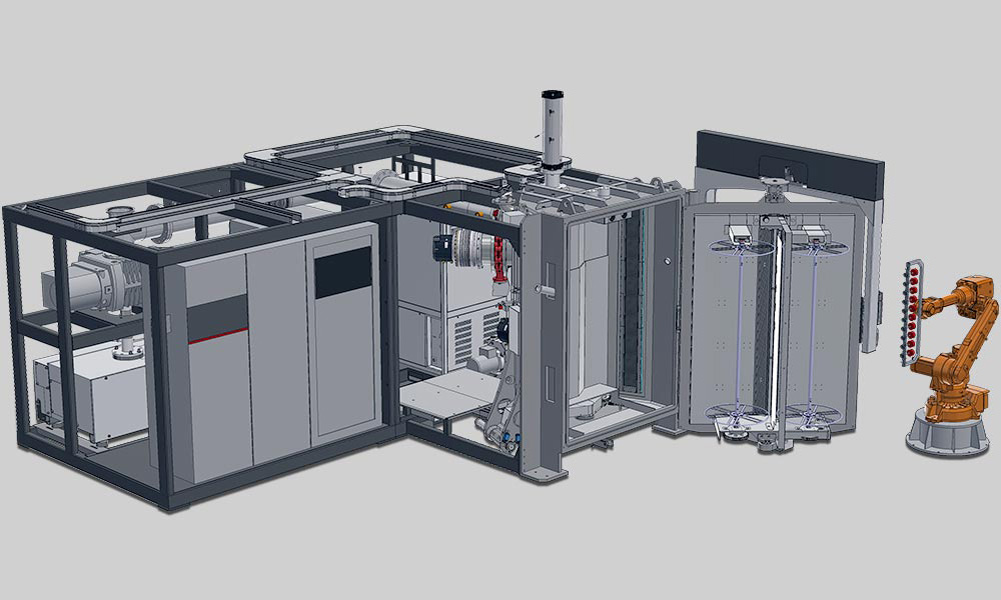
Schema di alcuni degli impianti Fast-Met per la metallizzazione e/o lo sputtering in alto vuoto utilizzati nello stabilimento Forvia Hella di Irapuato. Questi impianti, in diverse configurazioni, sono utilizzate dall’azienda per rivestimenti sia tecnici (fanali) sia estetici (tipicamente per componenti per interni auto). In via generale gli impianti Fast-Met possono rivestire con qualunque metallo, creando anche superfici colorate e/o semi-trasparenti. Le caratteristiche tecniche principali dell’impianto che ci è stato espressamente segnalato da Simon Peter Bott (Fast-Met II Double Face, con una singola stazione di lavoro di carico/scarico, che può essere facilmente automatizzata) sono le seguenti:
- dimensioni della camera (L x W x H): 1400 x 700 x 1900 mm
- numero di attrezzi: 2 per lato della stazione di lavoro.
- diametro degli attrezzi: 560 mm
- altezza utile: 1500 mm
- layout (L x W x H): 6000 x 5400 x 2200 mm
- tempo di ciclo: 4 – 8 minuti.
PVD E HARD COATING. IL REPARTO AD ALTA AUTOMAZIONE IN LINEA
«La linea PVD automatica (Arzuffi Line-Met) è il fulcro di un reparto altamente automatizzato che ci permette di depositare selettivamente il rivestimento per ottenere le ottiche (il cuore funzionale dei fari) con gli standard qualitativi più elevati a livello internazionale. Il reparto consta di macchine di stampaggio, un sistema di trasporto per mezzo di AGV gestito da una rete senza fili, una zona di mascheratura, una linea PVD e un’area di scarico e controllo qualità. Tutte le fasi sono robotizzate.
Una volta stampati, i pezzi vengono posti in vassoi appositi che vengono trasportati autonomamente dagli AGV alla zona di mascheratura e carico della linea PVD. Nella zona di mascheratura, un robot provvede al posizionamento delle maschere e al loro fissaggio. Terminata l’operazione, un secondo robot posiziona il vassoio nella stazione di carico della linea PVD.
La linea effettua in maniera totalmente automatica le seguenti operazioni in sequenza, passo a passo:
- svuotamento della camera (si genera il vuoto necessario per le fasi successive)
- plasma etching. In questa fase si effettua un pretrattamento a mezzo plasma delle superfici dei pezzi (pulizia da eventuali contaminazioni organiche e attivazione)
- sputtering (deposizione fisica del metallo)
- applicazione e polimerizzazione mediante plasma sottovuoto di un rivestimento protettivo ad alta trasparenza delle superfici metallizzate a scala nanometrica
- camera di ristabilimento della pressione atmosferica
- rimozione robotizzata delle maschere e loro posizionamento nell’apposito magazzino, invio dei vassoi alle stazioni di controllo qualità, che viene effettuato pezzo per pezzo.
Le camere 2, 3 e 4 sono mantenute costantemente nelle condizioni di vuoto previste. La camera 1 effettua il vuoto, mentre la camera 4 riporta la pressione alle condizioni atmosferiche. In questo caso è stato scelto di installare una macchina passo a passo per la forma dei pezzi che vanno rivestiti e per le “finestre” di passaggio del metallo sublimato (di grande precisione). Per ottenere la deposizione sui pezzi da rivestire, utilizziamo un doppio target (ciascuno composto dal metallo bombardato da argon). In un altro stabilimento del gruppo è invece presente una linea che effettua il processo di PVD dinamicamente (con i pezzi in movimento continuo nella camera di PVD).
Il software di gestione dell’impianto permette di intervenire su tutti i parametri chiave, come il livello di vuoto, le potenze applicate, le tempistiche e il tipo di metallo o di metalli depositati. L’operatore ha il controllo completo del processo tramite monitor grafico.
Poiché le camere di processo rimangono chiuse a lungo, non è necessario utilizzare “trappole d’umidità” (come avviene per gli impianti a batch).
Le camere 2, 3 e 4 sono mantenute in condizioni di vuoto con una pompa specifica turbomolecolare che non utilizza oli, ha un basso consumo energetico e richiede una limitata attività manutentiva. Il circuito è isolato rispetto a quello di svuotamento della prima camera, che invece utilizza una pompa a diffusione. L’impianto è dotato di un doppio circuito di raffreddamento che consente di regolare con precisione le temperature di processo. La camera di PVD è facilmente accessibile per sostituire i target.
Nel caso in esame, l’impianto è stato programmato per assorbire i flussi di produzione provenienti dal reparto di stampaggio. Il tempo di attraversamento della linea di ogni vassoio è compreso tra i 40 e i 50 secondi.
Le maschere (in materiale polimerico termoindurente) sono inviate, dopo un numero prestabilito di cicli, a una lavatrice a ultrasuoni per eliminare i rivestimenti e riportarle alle condizioni iniziali.
«Data l’alta automazione del processo, dallo stampaggio fino ai processi di PVD, e in considerazione degli alti standard qualitativi richiesti dai nostri clienti, in questo reparto la manutenzione dev’essere effettuata in modo molto diligente».
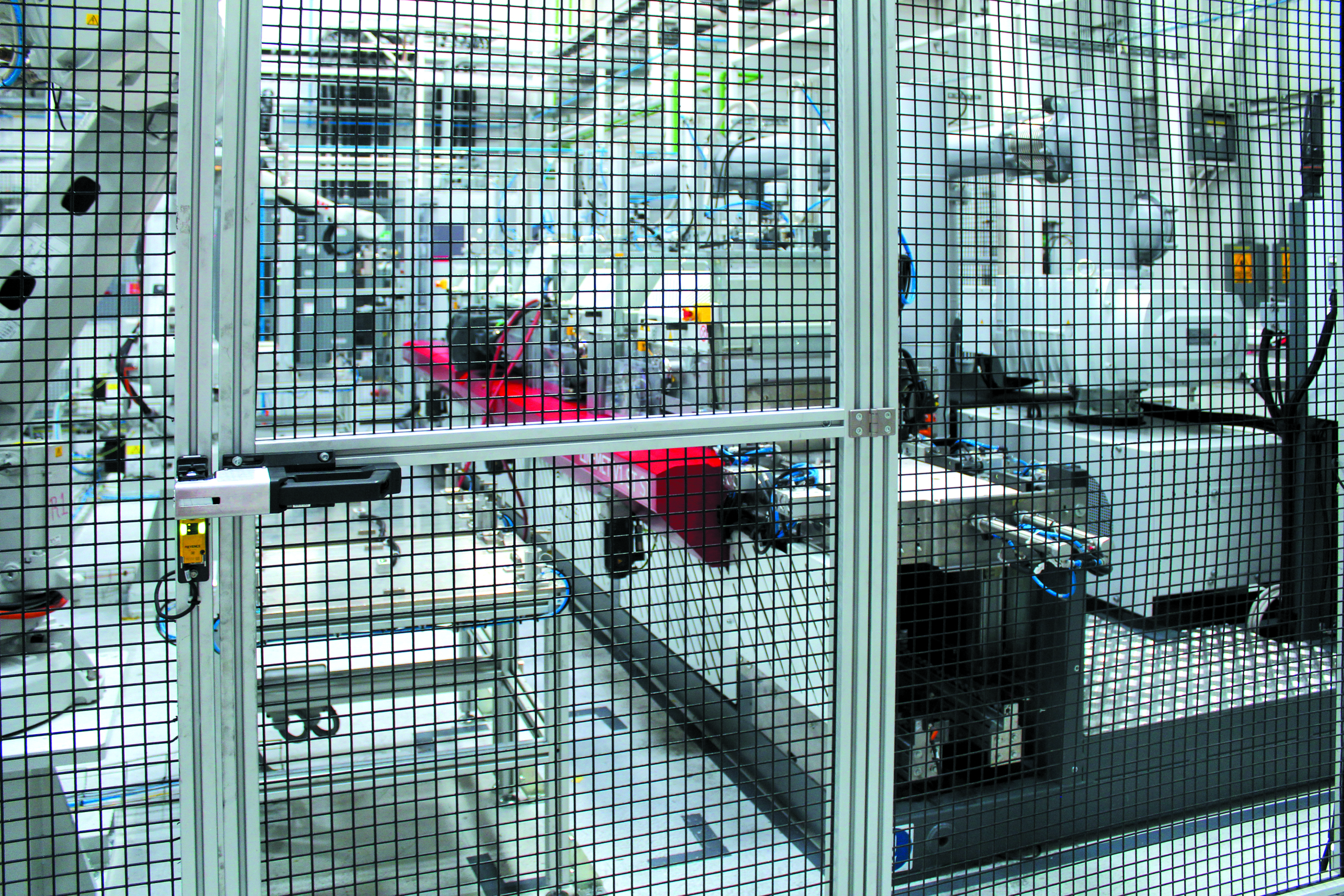
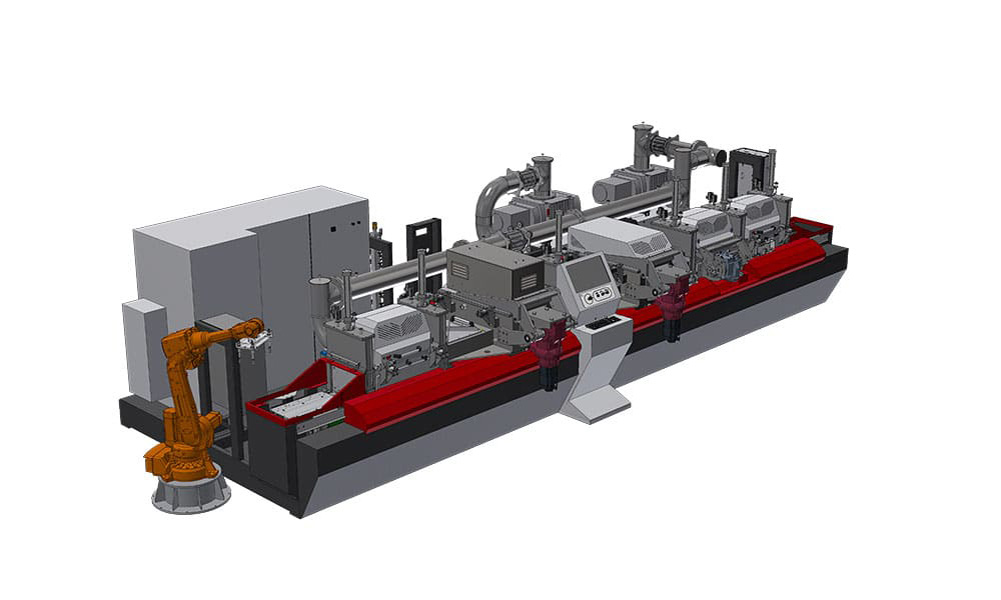
Una vista della Arzuffi Line-Met in fase operativa e lo schema dell’impianto installato nello stabilimento Forvia Hella visitato. L’impianto nasce da un progetto modulare, dal quale si possono ottenere differenti configurazioni. Queste sono le sue caratteristiche principali (in grassetto la configurazione scelta da Forvia Hella per lo stabilimento visitato):
- Area utile metallizzabile: 530 x 330 x 225 mm
- Attrezzi: vassoi
- Adattabilità: Adatto ad ottenere alta riflettività
- Tecnologie di rivestimento: scarica ionica – sputtering (deposizione statica) – sputtering reattivo – AHC (Arzuffi hard coating) – PECVD (HMDSO)
- Tempo di ciclo: 40-50 secondi.
CONCLUSIONI
«Circa 10 anni fa, in Hella – conclude Simon Peter Bott – abbiamo preso in considerazione la possibilità di minimizzare o evitare la manipolazione dei pezzi dopo il loro stampaggio. Sono state sviluppate varie ipotesi su come poter passare direttamente dalla fase di stampaggio a quella di metallizzazione. Alcune di queste ipotesi, per esempio il passaggio diretto dalla macchina di stampaggio alla camera di metallizzazione tramite robot, hanno mostrato problemi tecnici non superabili, come l’elevata temperatura del pezzo subito dopo lo stampaggio, i tassi di ritiro differenti del materiale plastico e del metallo depositato. Abbiamo coinvolto nello studio alcuni fornitori di impianti PVD e installato i prototipi delle due soluzioni che ci sembravano più promettenti: un impianto con camera di grandi dimensioni, capace di ricevere direttamente dalle macchine di stampaggio un elevato numero di pezzi che, nell’attesa del suo completo riempimento, potevano raffreddarsi, e il sistema in linea sviluppato da Arzuffi. L’ultima soluzione mostrava un vantaggio economico significativo, in quanto richiedeva un minor numero di pompe e di capacità inferiore, dato che non era necessario creare il vuoto per l’intero volume di una camera grande, ma solo per la precamera, una volta effettuato il vuoto nelle camere di processo, che doveva solo essere mantenuto nel tempo. Questa soluzione richiede pompe di capacità inferiore che operano per tempi inferiori. In definitiva, un impianto più economico sia in termini di investimento iniziale, sia di processo.
Il rapporto con Arzuffi PVD ha permesso un’evoluzione continua dell’idea iniziale: abbiamo trovato disponibilità all’ascolto, allo studio e all’introduzione delle modifiche che si rivelavano migliorative nel tempo e un servizio all’altezza delle nostre aspettative. Infine, poco meno di due anni fa, abbiamo messo in funzione questo reparto che soddisfa l’obiettivo iniziale di minimizzare la manipolazione dei pezzi, generare un flusso continuo e integrato di pezzi metallizzati, garantire una capacità di risposta flessibile alle esigenze del mercato e mantenere una cadenza produttiva stabile e di qualità».